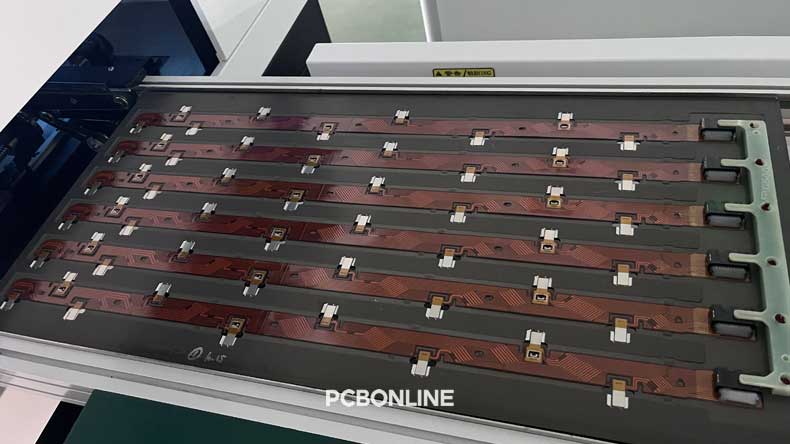
Electronic products are getting smaller. Due to the limited assembly space, many devices use SMDs (surface-mount devices) mounted on FPC (flexible printed circuit) for electronics assembly. FPC is widely used in mobile phones, cameras, display screens, wearable electronics, etc. Let's dive into the FPC SMT manufacturing process and learn everything about it.
Overview of FPC
FPC, also known as flexible PCB, is a highly reliable flexible printed circuit made of PI (polyimide) or PET (polyester) film.
According to the definition of JIS C5017, FPC is a single-sided flexible printed circuit board that uses copper foil to form a single-sided circuit on a PET or PI substrate or a double-sided flexible printed circuit board that uses PI as the substrate to form circuits on both sides.
You can view the pros and cons of FPC from the table below.
Pros
|
Cons
|
Lightweight, compact, and thin
|
Longer manufacturing process than rigid PCB, higher cost
|
Flexible, can move and extend in 3D space
|
Higher scrap rate than rigid PCB in manufacturing
|
Larger design area, three-dimensional wiring possible
|
Low mechanical strength
|
Good thermal dissipation
|
Quality inspections to FPC are more difficult than PCB
|
Can improve wiring density
|
Require custom jigs for manufacturing and assembly of the FPC
|
At the one-stop FPC manufacturer PCBONLINE, you can have FPC manufactured and assembled. PCBONLINE has an FCCL (flexible copper-clad laminate) factory to produce the FCCL and coverlay required for FPC manufacturing. Later, it manufactures the FPC in its advanced PCB manufacturing bases and assembles them to be printed circuit assemblies in its PCB assembly factory.
You can see the FPC manufacturing capabilities at PCBONLINE:
FPC Specs
|
PCBONLINE Capabilities
|
|
Circuit layer
|
1 to 8 for PI FPC, 1 to 6 for PET FPC
|
|
FPC thickness
|
Limit: 0.05mm
0.1-0.5mm (1-4L) 0.6-0.8mm (5-8L) |
|
Tolerance of 1L FPC thickness (exclude stiffener)
|
±0.03mm
|
|
Tolerance of 2L FPC ≤0.3mm thickness (exclude stiffener)
|
±0.03mm
(Normal ±0.05mm) |
|
Tolerance of multilayer FPC <0.3mm thickness (exclude stiffener)
|
±0.03mm
(Normal ±0.05mm) |
|
Tolerance of multilayer FPC 0.3mm-0.8mm thickness (exclude stiffener)
|
±10%
(Normal ±0.1mm) |
|
Tolerance of FPC thickness (include PI stiffener)
|
±10%
(Normal ±0.05mm) |
|
Tolerance of FPC thickness (include FR4 stiffener)
|
±10%
(Normal ±0.1mm) |
|
Maximum finished FPC size
|
7.8inch*21.8inch (PI≥1mil)
7.8inch*14inch (normal) |
|
Minimum finished FPC size
|
2mm*4mm (no connection tab)
8mm*8mm (with connection tab) |
|
FPC Material
|
Adhesive flex core |
SF305: PI=0.5mil, 1mil, 2mil; Cu=0.33OZ, 0.5OZ, 1OZ
|
Adhesiveless core |
Panasonic RF-775(Electrode Posited Copper):PI=1mil,2mil;Cu=0.33,oz0.5,1oz, 2oz
|
|
DuPont AP:PI=1mil,2mil,3mil,4mil;Cu=0.5oz,1oz, 2oz |
||
Coverlay |
SF305C series: 0515,0525,1025,1035, 2030 |
|
TaiFlex FHK series: 0515, 0525, 1025, 1035, 2025 |
||
Thermosetting adhesive |
TaiFlex series:AD=10um,25um,40um
|
|
ShengyiSF302B:AD=25um,40um |
||
PI stiffener |
TaiFlex MHK series: PI=3mil, 5mil, 7mil, 9mil
|
|
3M tape |
9077, 9460
|
FPC SMT Methods - Roll-to-Roll and Attachment with Jig
To ensure success of FPC SMT manufacturing, the key is to fix and locate the board. As the FPC board is soft, it cannot be fixed and transmitted without a special carrier, which is called a jig, to complete the SMT processes, such as solder paste printing, placing SMDs, and passing the reflow oven.
Below, you can see two manufacturing methods for FPC SMT and their pros and cons: one is the less-used Roll-to-roll method, and the other is the most common and mature jig method.
Roll-to-roll method
Pros:
- Doesn't require attaching the FPC to the jig
- Prevents creases and scratches on the FPC
- Avoids contamination of the FPC due to personnel operations and the environment, making it suitable for products that require a dust-free production environment
- Simplifies packaging, transportation, and manufacturing operations
- Can meet the COF (Chip-on-Flex) process requirements of ultra-thin and high-end FPC
Cons:
- Equipment on the production line is specialized and applicable to a narrow range of products
- The investment cost of roll-to-roll production equipment is high
- Only suitable for ultra-large-scale FPC production. Not suitable for small-batch production mode
The roll-to-roll or reel-to-reel manufacturing method for FPC is a continuous production process where the flexible PCB sheet is assembled with SMDs in a roll rather than individual pieces. The roll-to-roll FPC SMT process includes: baking to unwind the FPC roll, feeding the FPC roll into the SMT line, solder paste application, component placement, reflow soldering, AOI automated optical production, visual inspection, rewinding, and cutting to make them into individual units.
FPC SMT Using a Jig
Pros:
- Easy integration with standard SMT lines thereby simplifies automation
- Cost-effective for small and medium-volume
- Easier inspection and testing
- The jigs can be reused and adaptable for other FPCs in similar sizes and shapes
Cons:
- Manual load and unload thereby limited automation and lower efficiency
- Require custom jig design and manufacturing
- Complexity in double-sided FPC SMT
The FPC SMT method of using a jig is securing the FPC on a rigid fixture to facilitate component placement and inspection. The FPC SMT process using a jig includes: baking to unwind the FPC, securing the FPC onto the jig, solder paste application, component placement, reflow soldering, releasing the FPC, and visual inspection.
Details of FPC SMT Process of the Attachment with Jig Method
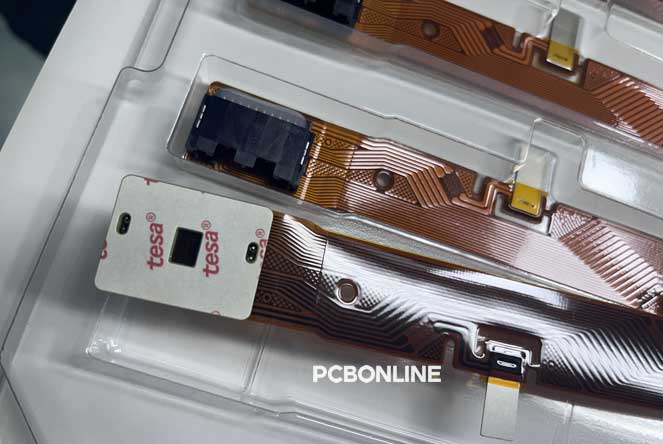
FPC SMT using a jig is the most versatile assembly for flexible PCBs. There are many details for you to learn about. Let's explore them one by one.
Jig types for FPC SMT
The jig for FPC SMT ensures the FPC is flat during the assembly process. It needs to be thin, high-strength, absorb less heat, dissipate heat quickly, and have little warping and deformation after multiple thermal shocks. The jig materials include synthetic stone (engineering plastics), aluminum, silicone, and special high-temperature-resistant magnetized steel.
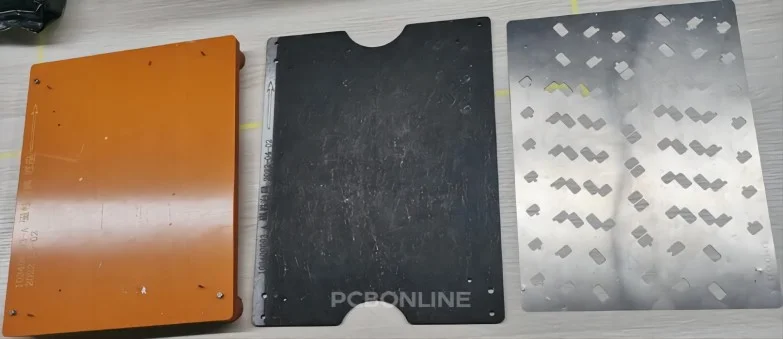
Synthetic stone (engineering plastics): convenient design and manufacturing. The service life of engineering plastic jigs is 3000-7000 times. They are easy to operate, have good stability, are not easy to absorb heat, and are not hot to the touch. The price is 5 times of aluminum jigs.
Aluminum jig: It absorbs and dissipates heat quickly. There is no temperature difference inside and outside, and the deformation can be easily repaired. It is cheap and has a long service life. The main disadvantage is that it is hot to the touch and requires heat-insulating gloves to pick it up and transport it.
Silicone jig: Silicone is self-adhesive and resistant to high temperatures. The FPC can be directly attached to it, and it is easy to release the FPC from it. During FPC assembly, the silicone material ages, and its viscosity decreases. Therefore, its service life is short, at most 1000-2000 times, and the price is relatively high.
Special high-temperature resistant magnetized steel jig: This jig is a special high-temperature resistant (350℃) steel sheet magnetized to ensure a "permanent magnet." It has good elasticity, good flatness, and no deformation during reflow soldering. It presses and flattens the surface of the FPC, ensures FPC soldering quality, and improves the yield rate. It can be used permanently. The magnetic fixture also provides heat insulation protection for the FPC. However, it has a high unit price and has cost advantages only in mass production.
Baking FPC before SMT assembly
FPC materials can absorb moisture. If they are not baked, the damp FPC will pop and delaminate after reflow soldering, resulting in scrap. Therefore, the FPC needs to be baked before assembly.
The FPC baking conditions need to be set based on the FPC material, FPC thickness, oven, baking tray, etc. After engineering experiments, the baking temperature, baking time, and stacking quantity are set.
After baking, the FPC needs to be cooled to room temperature before it can be put into SMT production. Otherwise, the hot FPC will cause a thermal collapse of the solder paste. The cooling time and overdue re-baking time should be determined after engineering experiments.
Solder paste application
FPC does not require special compositions of solder paste. The size and metal content of the solder powders should be selected based on whether there is a fine-pitch IC on the FPC.
However, FPC SMT requires the solder paste to have excellent printing performance. The solder paste should be easy to print and firmly adhere to the FPC surface without blocking the steel holes or collapsing after printing.
As the printed surface of the FPC cannot be as flat and consistent in thickness and hardness as the rigid PCB, it is not suitable to use a metal scraper but a polyurethane scraper with a hardness of 80%-90%.
Besides, the solder paste printing machine should have an optical positioning system to ensure the printing quality. The setting of the equipment parameters can also impact the printing effect.
Component placement
As the SMD quantity on the FPC is small, for efficiency, PCB panelization is often required for FPC SMT. Multiple FPCs are secured on the jig for component mounting. During component placement, the arms of the SMT mounting machine pick and place the same SMD on each FPC at one time.
Reflow soldering
FPC SMT reflow soldering requires to use of a forced hot air convection infrared reflow soldering oven for uniform temperature changes on the FPC.
The setting of the reflow profile impacts the soldering effect. In the testing stage, the engineers at PCBONLINE will attach two temperature probes at two ends of the testing board near the solder joints to inspect the temperatures for setting up a proper reflow profile.
Based on our FPC SMT experience, we usually adjust the reflow temperature to the low limit of the solder paste. The wind speed of the reflow oven is the lowest speed that the oven can adopt. The chain stability of the reflow furnace should be good without shaking.
Inspection of the FPC assembly
After reflow soldering, the FPCs on the jig pass the AOI automated optical inspection machine for inspection. For high-end FPC SMT, such as the cell contact system, the AOI is three-dimensional, and then the FPC assembly also needs to go through the X-ray machine for inspection.
One-stop FPC SMT Manufacturer PCBONLINE
For high-quality FPC manufacturing and assembly at one stop, you can work with the FPC SMT manufacturer PCBONLINE. PCBONLINE has an FCCL factory to provide the sheet and coverlay for FPC manufacturing, two large advanced PCB manufacturing bases, and one PCB assembly factory for FPC SMT manufacturing.
PCBONLINE gains a high yield rate of FPC manufacturing and assembly with more than 24 years of experience.
High-quality FPC SMT certified with ISO 9001:2015, IATF 16949:2016, RoHS, REACH, UL, and IPC-A-610 Class 2/3.
Affordable FPC SMT manufacturing as PCBONLINE is a source factory manufacturer producing the FCCL, FPC, and assemblies.
PCBONLINE provides DFM (design for manufacturing) before and during PCBA prototyping to ensure the success of your product and avoid potential economic losses.
For bulk FPC SMT production, PCBONLINE offers free samples, R&D, and PCBA functional testing.
No matter what application your FPC is designed for, PCBONLINE can bring your idea into reality and offers one-on-one engineering support throughout the project. To get a quote from PCBONLINE, please email info@pcbonline.com.
Conclusion
This blog gives an overview of FPC and reveals details of FPC SMT. The biggest difference between FPC SMT and rigid PCB assembly is that it requires a jig to secure it during assembly. To get cost-effective and high-quality FPC SMT manufacturing, don't hesitate to work with PCBONLINE.
CCS Product Introduction - PCBONLINE.pdf