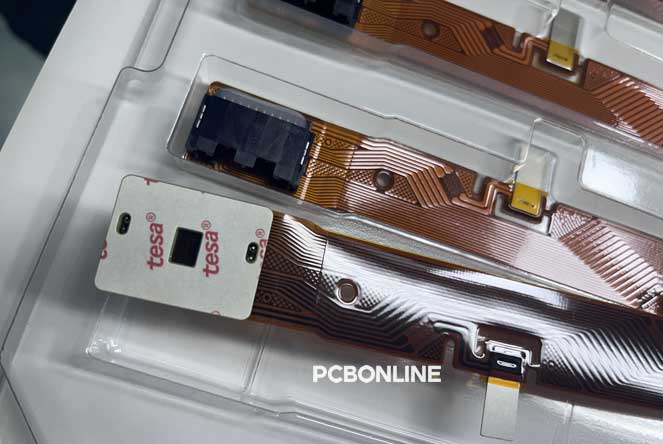
Flexible printed circuit boards, also known as FPCs, provide flexibility and save space for applications. When electronic components are mounted on a flexible PCB, this PCB assembly is a flex PCBA.
Flex PCBA is trendy as compact and flexible devices and modules are put in more and more use. It solders SMDs (surface-mount devices) and connects them electrically. After the SMT assembly, the flex PCBA becomes a module, or it can further be processed to assemble with other components to be a system.
To explore more about flex PCBA, read the below content.
In this article:
Part 1: Applications of Flex PCBA Part 2: Benefits of Flex PCBA Part 3: FPC Materials for Flex PCBA Part 4: How to Custom Make Flex PCBA Part 5: Flex PCB Design Part 6: Flex PCB Fabrication Part 7: Flex PCB Assembly Part 8: Flexible PCBA tests Part 9: Flex PCBA Manufacturer from R&D to Manufacturing and Box-Build AssemblyApplications of Flex PCBA
Anywhere with compact space that needs circuit connection and flexibility can use a flex PCBA. Especially, they are used in the covers, corners, sides, and screens of aerospace, automotive, computer, communication, and medical electronics.
Here are some flex PCBA applications.
Cell contact system for EV battery packs
In the lithium-ion battery pack for EVs and HEVs, there is a cell contact system (CCS) that connects the battery cells and the BMS (battery management system). Flex PCBA provides a mature solution for CCS.
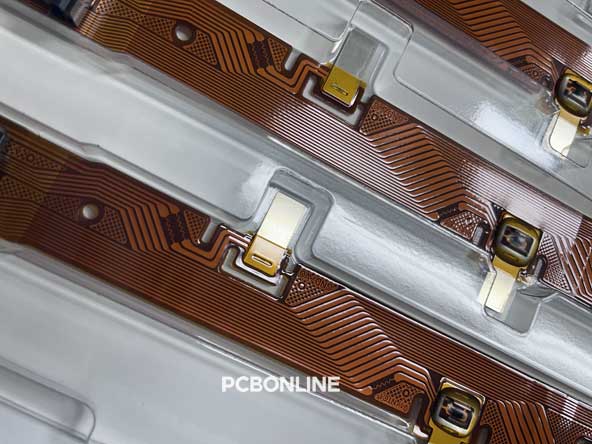
On the flex PCBA for the battery CCS, there are NTCs (thermistors), nickel sheets, and connectors surface mounted.
The flex PCBA collects and monitors the temperature changes of the battery cells and reflects them to the BMS through the circuit changes.
Besides, the CCS is the component for slow-charging the EVs and HEVs.
Also, during charging the vehicles, the flex PCBA CCS monitors the battery power and tells the BMS which cell is not fully charged.
The flex PCBA CCS is usually designed on the cover of the EV battery pack. Using flex PCBA as the CCS greatly saves space and reduces weight for the vehicles.
Buttons of the smartphones
In every smartphone, there are buttons on the right side. They are the main and volume control buttons. Under the enclosure, There is a flex PCBA on the right side to mount the buttons and connect the circuits.
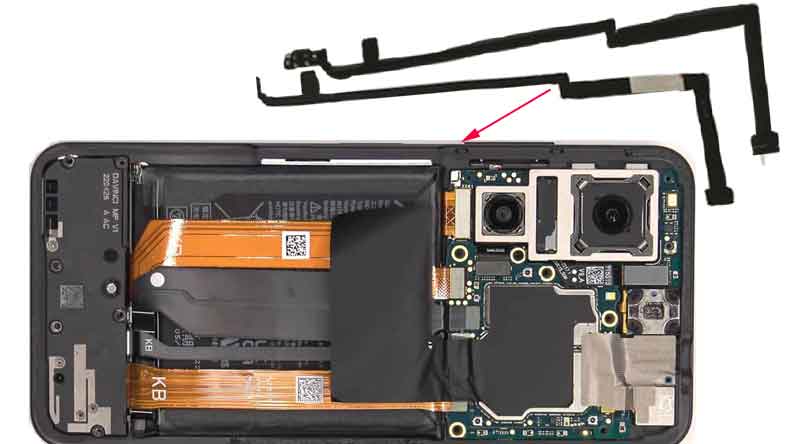
For some smartphones, the main button is at the footer of the screen. There is also a flex PCBA for the button.
Screen displays for computers, mobile phones, automotive LED screens
For all kinds of computers, mobile phones, tablets, and automotive smart terminals, their LED screen can be considered as a flex PCBA. This is because the LED screen is connected by or soldered on a flexible PCB for circuit connection.
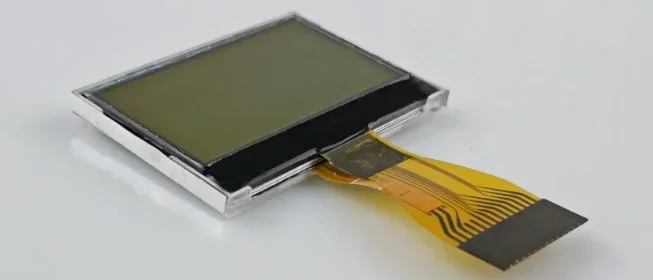
For laptops where the screen is opened and closed multiple times in use, the flex PCBA that connects the screen and the mainboard is a rigid-flex PCB assembly.
Sensors for automotive, defense, aerospace, and medical
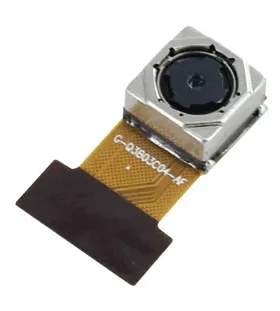
All kinds of sensors, such as infrared, pressure, position, temperature, acceleration, angular velocity, flow, gas concentration, and liquid level sensors, can be flexible PCBA modules. They are widely used in automotive, defense, aerospace, and medical electronics.
The sensor is mounted on the flex PCB as a sensor module. The module can be installed in the system or device.
Flexible LED strips
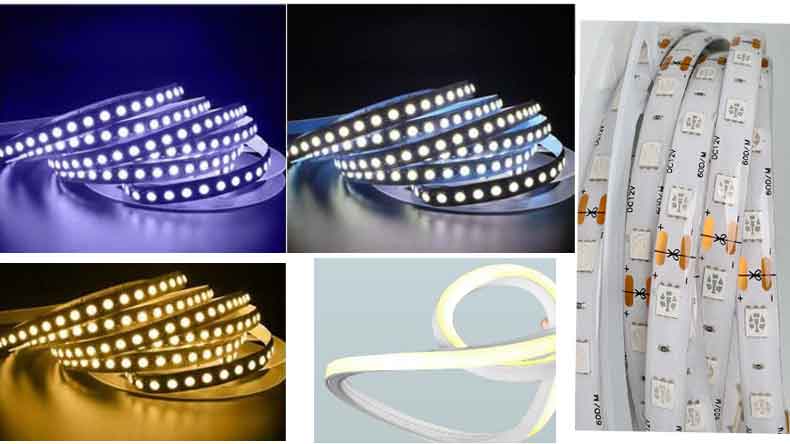
Flexible LED strips are made of flex PCBA covered with waterproof plastic film. The LEDs are surface-mounted on a flexible PCB.
Due to the series connection, the maximum length of a flexible LED strip PCBA is 200m.
Benefits of Flex PCBA
A flex PCBA is a flexible printed circuit assembly using surface-mount devices to mount on a flexible circuit board. The flex circuit board uses PI (polyimide) or PET (polyester) copper-clad laminate. It can conform to desired shapes according to the application.
The Flex PCBA offers the following benefits:
- Flexibility: FPCs offer the freedom to design and integrate circuits into unconventional shapes.
- Space saving: Flex PCBA is thin and lightweight. This makes it ideal for compact electronic devices.
- Reduced weight: FPC assemblies are lightweight, which is crucial for aerospace and automotive.
- Finer circuitry: At the flex PCBA manufacturer PCBONLINE, the minimum trace width and space are both 0.05mm. Compared with rigid PCBA, flex PCBA has finer circuits, helping high-density interconnects.
- Different types of flex circuits (IPC 6013 Types 1-4) cater to various needs: IPC 6013 Type 1 flex PCBA is single-sided for simple applications. IPC 6103 Type 2 flex PCBA is double-sided for more complex applications. IPC 6103 Type 3 flex PCBA is a multilayer for high-density-interconnect and high-speed applications. IPC 6103 Type 4 flex PCBA is a multilayer rigid-flex for communication applications.
FPC Materials for Flex PCBA
Polyimide (PI) or polyester (PET) films are the PCB materials for flex PCBAs. They are used as the substrate and insulating layers of transparent flexible PCB. They can bend, and fold, and are easy to install, offering high reliability and flexibility.
PI has high and low-temperature resistance, electrical insulation, adhesion, radiation resistance, and medium resistance. PI flex PCBAs are commonly used for flexible applications. The following image shows the PI film used as the insulator in FPC.
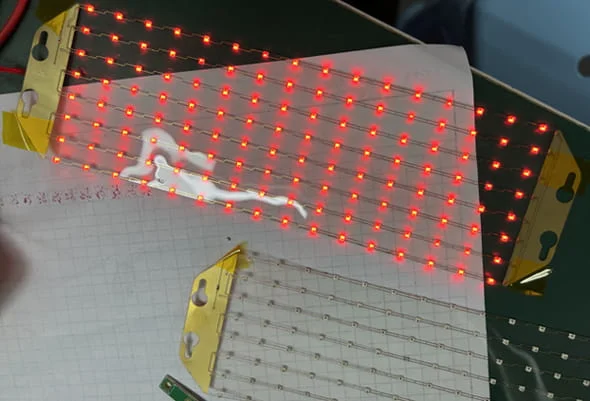
PET film is the insulation film used for transparent flexible PCBs. Its transparency can reach 90%. However, PET is not resistant to high temperatures. For this reason, silver surface finishes are used in the transparent flex PCB, and the reflow soldering for transparent flex PCBA is low-temperature. The following image shows the transparent FPC using PET material.
How to Custom Make Flex PCBA
To custom make a custom Flex PCBA, the following processes are necessary:
1. FPC Design
2. FPC Fabrication
3. Flex PCB assembly
4. FPC assembly testing
Following are the detailed guidelines.
Flex PCB Design
1. Understand the required electrical parameters, including current maximums, voltages, signal types, capacitance limitations, impedance characteristics, and shielding considerations.
2. Begin by creating the schematic, which serves as the initial representation and design of the circuit board.
3. Utilize any schematic capture tool like Proteus or Altium to design the PCB layout. This allows visualization of the board's appearance, operation, and component placement.
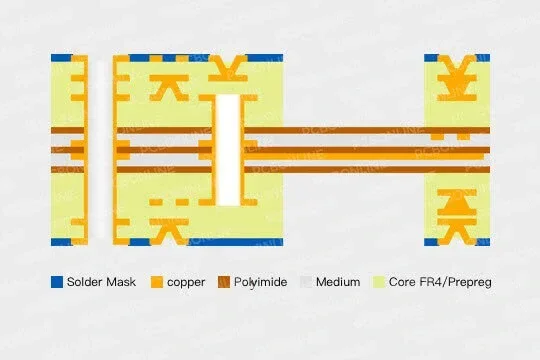
4. Develop the flex PCB stackup early in the design stage to address impedance concerns.
5. Incorporate drill holes as determined by component connections.
6. Proceed to route the traces, connecting segments of the circuit path following component placement and drill hole insertion.
7. Add labels, identifiers, markings, and reference designators to the layout.
8. Generate design/layout files containing all necessary information for flexible PCB fabrication, manufacturing, and assembly.
Design rules
The important design rules for flex PCB are:
A. Choosing the right materials is crucial for flex PCBs. Opt for substrates with good flexibility and thermal stability, such as PI or PET films. Additionally, consider the material's dielectric properties, thickness, and compatibility with your specific application requirements.
Generally, the polyimide material with Dk of 3.2 to 3.4 is selected for FPCs.
B. Flex PCBs offer numerous advantages over rigid boards, such as reduced weight, space-saving, and enhanced durability. Therefore, to ensure flexibility, use adhesive-less material.
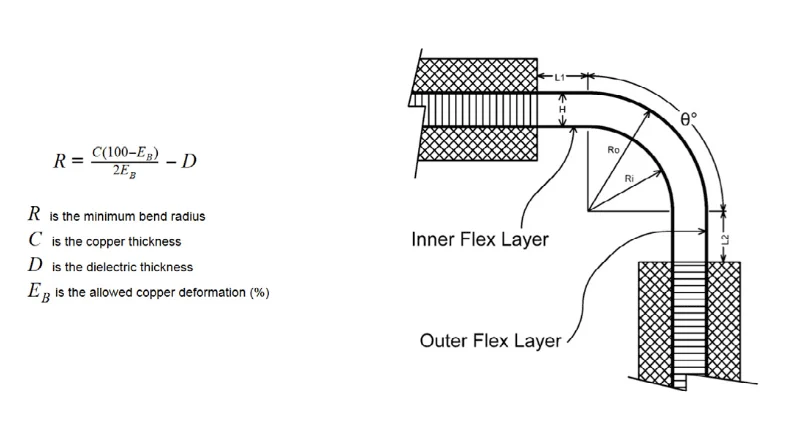
C. Bend-ability is an important factor in FPC, thus it is vital to understand what bend radius is. The bend radius is the degree up to which the flex area of FPC can flex. Set the bend radius based on the measurement of the inside surface of the bend to ensure the extent of flex as required.
D. When the layout is being prepared for the bend area of flex PCB, avoid using 90-degree bends. Instead, use large curved angles.
E. Similarly, a distance of 0.5mm should be maintained between plated through holes (PTHs) and the bend area.
F. For adding Vias, set the angular ring diameter to at least 10mil.
By considering these key factors – a robust and reliable flex PCB design can be created.
Flex PCB Fabrication
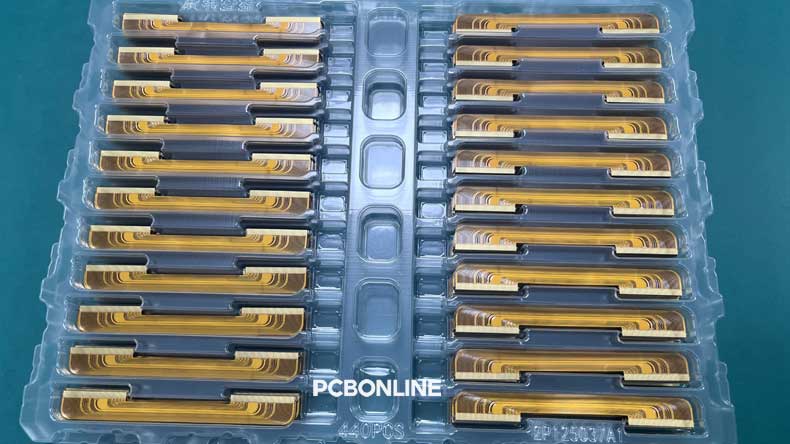
Step 1. First of all, the copper foil is pressed to the required thickness to make flexible PCB laminates.
Step 2. The copper laminate is then laser-drilled for Plating Through Hole (PTH).
Step 3. Once the PTHs are drilled, these holes are electroplated with copper on the vertical continuous plating (VCP) line.
Step 4. Then the UV-sensitive photoresist is applied to the laminate, and a film with the circuit image is exposed.
Step 5. The non-circuit copper areas are solved, leaving behind circuit traces and pads after the etching process.
Step 6. At last positioning holes are drilled using mechanical drilling.
Step 7. For the final touches, the residual moisture and oxide layer is removed. After that, the silkscreen is baked for drying, and a surface finish is applied to the exposed copper pads.
Step 8. Finally, electrical testing is done to ensure circuit functionality.
Flex PCB Assembly
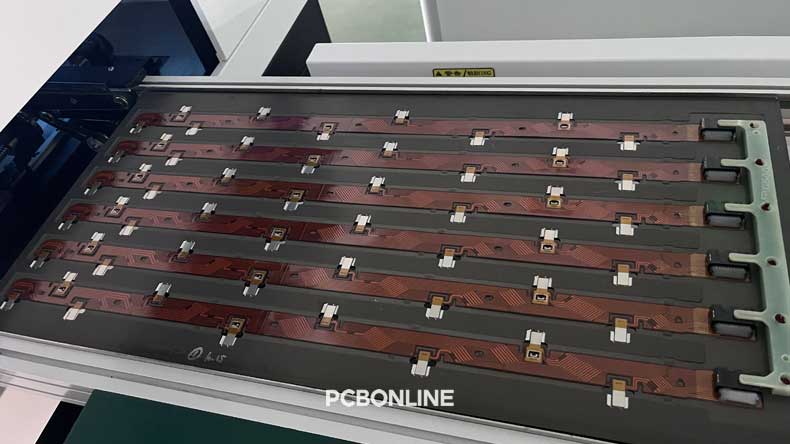
Flexible PCBs offer unique advantages with their lightweight and bendable nature, but their assembly presents challenges such as securing boards during Surface Mount Technology (SMT) assembly. Flex circuit assembly involves SMT assembly of flexible printed circuit boards (FPC), where electronic components are surface-mounted.
In the beginning, secure the flex PCB panel by putting it in a jig.
After that, complete the normal SMT assembly steps, including solder paste silkscreen printing, solder paste inspection, component placement, reflow soldering, and automated optical inspection.
To ensure the quality of flexible PCB assemblies, manufacturers conduct various tests like tension testing, button strike life testing, bending testing, environmental protection testing, etc.
Flexible PCBA tests
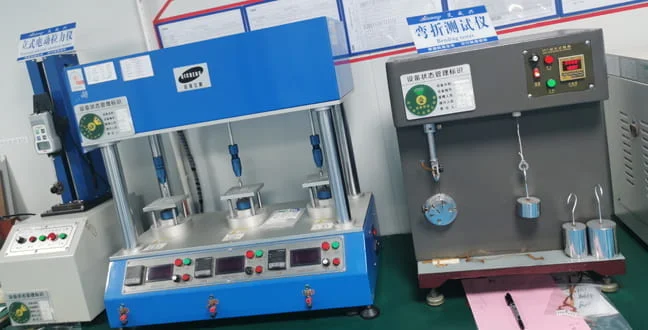
Following are some tests that are conducted on flex PCBAs for quality assurance.
- Tension testing: This test evaluates the flex PCBA module's stretching capabilities because the flexible PCBA needs to be stretchable to be used.
- Button strike life testing: A button strike life tester is used. It tests out the maximum number of strikes a button on FPC can withstand.
- Bending testing: An important quality of a flex PCBA is its bendability. To ensure the flex PCBA's bending radius meets the application requirements, the bending test is conducted.
- Hand sweat testing: This test ensures that the impact of hand touches during production and assembly is minimal to none on the quality of the PCBA.
- Environmental protection test: To guarantee the reliability of FPC assembly, environmental testing is done in different temperature environments. Similarly, salt spray testing is conducted for modules that will find their application in high-salinity environments.
- Pull strength test of solder joints: When the components are soldered on the FPCs, the pull strength testing is done to evaluate the solder joint and their strength after assembly.
- Electrical testing: This is done to detect any potential circuit issues, including fuse circuits. The bridge testing is used to measure the resistance, capacitance, and conductance of the flex PCBA.
Flex PCBA Manufacturer from R&D to Manufacturing and Box-Build Assembly
PCBONLINE is a one-stop flex PCBA manufacturer providing R&D, FPC fabrication, flex PCB assembly, PCBA value-added, and box-build assembly. You can have flex PCBA manufactured, tested, and made into systems and final products from PCBONLINE.
Founded in 1999, PCBONLINE has complete production lines for manufacturing FPC laminates, flexible PCB manufacturing, flex PCB assembly, box-build assembly, and even a specialized line for cell contact system assembly. Besides, PCBONLINE has an R&D team to provide ODM solutions and one-on-one engineering support throughout the way.
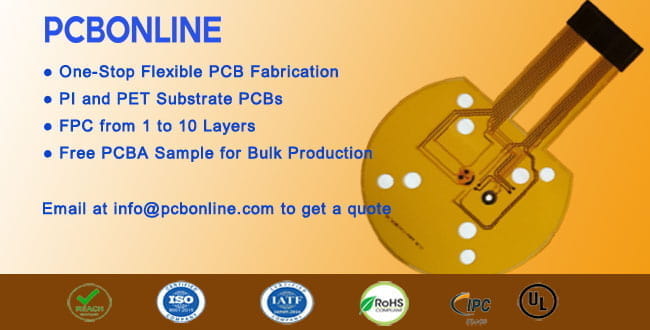
You can have flex PCBA designed and manufactured under one roof, including component sourcing, with no hassle.
PCBONLINE provides a wide range of flex PCBs, including single-sided, double-sided, 1 to 10-layer, transparent, and rigid-flex.
PCBONLINE assembles flexible PCBs to flex PCBA and modules and does comprehensive post-assembly tests.
After flex PCB assembly, PCBONLINE can further assemble it to be a flexible system or final product.
PCBONLINE provides flex PCBA manufacturing of high quality, following IPC-A 610 Class 2/3.
PCBONLINE has no minimum quantity limit for flex PCBA. But we encourage you to order from prototypes to batch production, offering free R&D, PCBA samples, and product prototypes for batch manufacturing orders.
We have manufactured flex PCBA and PCBA box-build assemblies for many applications, including CCS, sensor modules, flexible LED strips, etc, for automotive, medical, consumer, communication, computer, defense, and industrial devices. If you need flex PCBA, please send your inquiry by email to info@pcbonline.com.
Conclusion
This blog reveals flex PCBA from many aspects, from applications, and benefits, to design and manufacturing. The one-stop flex PCBA manufacturer PCBONLINE provides R&D, FPC fabrication, flex PCB assembly, and box-build assembly. If you have any questions about flex PCBA, feel free to chat with us from the online chat window.
PCB assembly at PCBONLINE.pdf