Heating is an important part of many industrial processes, including plastic molding, smelting, packaging, steam production, and chemical treatment. Therefore, precise temperature control is a critical requirement for quality assurance and occupational health and safety in modern industries.
Simple on/off heater control systems are inadequate for applications requiring variable heating. Hence, a custom heater control PCB (printed circuit board) is used to regulate temperature by controlling the electrical power supplied to the heater.
The heater control cards are often operated by feedback-based industrial control systems, such as programmable logic controllers (PLCs) or relay logic circuits. The controller receives real-time temperature feedback from temperature sensors (thermocouples or RTDs) and adjusts the power flow to the heater accordingly.
In this article, we will explore the functions, applications, circuit and PCB design, and PLC integration of industrial heater control cards/PCBs.
Overview of Heater Control Cards/PCBs
There are various types of industrial heaters, including tubular heaters, immersion heaters, ceramic heaters, infrared quartz heaters, and induction heaters.
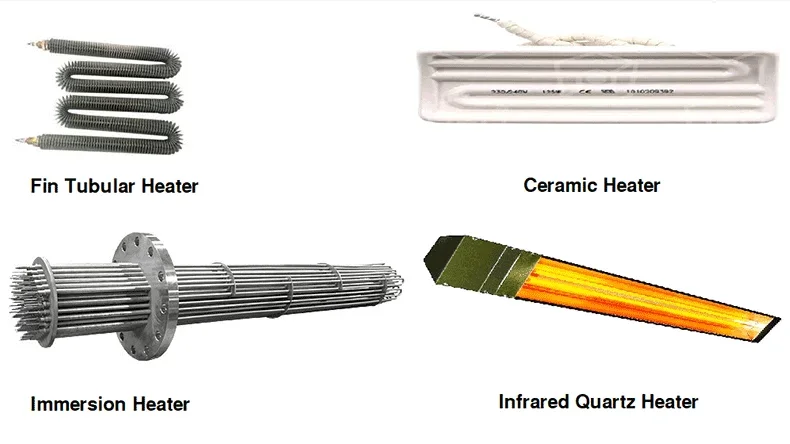
Different types of industrial heaters
All of these industrial heaters require a heater control card for precise temperature regulation in specialized industrial applications.
The heater control card is a custom printed circuit board designed to control the amount of power delivered to the heater based on temperature feedback and other process control requirements.
With its low-voltage control section and high-voltage power section, the heater control PCB serves as an intermediary between the heaters and the PLC, ensuring safe and efficient operation.
A typical PLC heater control PCB consists of:
- a control input section, where it receives control signals (digital or analog) from the PLC or other industrial controllers,
- a power output section containing solid-state relays (SSRs), TRIACs (Triode for Alternating Current), or IGBTs for power flow control,
- and an indication section for displaying system status, fault conditions, and communication activity.
Role of PLCs in Heating Control Applications
Programmable Logic Controllers (PLCs) are industrial computers designed to control input and output field devices in harsh industrial environments. They have become the de facto standard for automation tasks in industries around the world.
For temperature control applications, PLCs are integrated with heater control cards/PCBs to enable precise and accurate closed-loop temperature regulation. This integration not only automates the heating process but also enhances system safety and enables remote monitoring features.
In a typical industrial temperature control setup, the PLC reads data from temperature sensors and sends corresponding control signals to the heater control card/PCB.
The heater control PCB then modulates current flow to the heater to maintain the desired temperature.
PLCs can implement various control algorithms to achieve effective temperature regulation through the heater control PCB, with PID (Proportional-Integral-Derivative) control being one of the most widely used algorithms in temperature, level, pressure, and flow control applications.
Beyond temperature control, PLCs also handle critical safety functions such as emergency shutdowns, fault detection, and safety interlocks, making them a key component for reliable and efficient handling of industrial heating systems.
Key Features of PLC Heater Control PCB
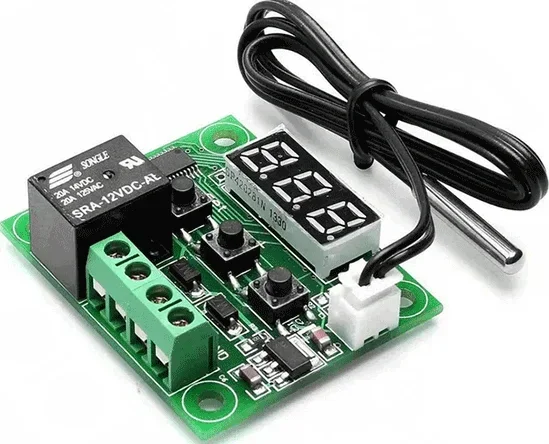
A custom heater control card/PCB
Below are the features of the custom PLC-controlled heater control PCB, regarding temperature regulation, on/off control, safety features, and output indications.
Temperature Regulation
Heater control cards play a key role in regulating heaters’ temperature. These custom PCBs receive commands from the PLC and adjust the power flow to the heater accordingly.
PLC-controlled heater control cards usually do not have built-in temperature sensors or setpoint tracking mechanisms.
This temperature regulation functional is typically achieved through external thermocouples or RTDs interfaced with the PLC.
Based on the sensor feedback, the PLC adjusts the heating temperature via the heater control card/PCB to match the predefined setpoint. A PID control algorithm is generally used to achieve and maintain the setpoint temperature.
On/Off Control
PLCs can provide basic on/off control of heater elements for simpler applications that do not require analog-range temperature control.
For the on/off control mechanism, the heater control card/PCB typically employs solid-state relays, electromechanical relays, or TRIACs to switch the power source on or off.
Advanced PLC algorithms implement hysteresis logic to prevent rapid on/off cycling of the heaters, which can lead to premature wear.
Safety Features
Heating systems pose a significant risk of fire incidents. Therefore, safety features are of utmost importance in heating control systems.
Taking this risk factor into consideration, the PLC heater control PCBs are designed with multiple safety features, including over-current protection, short-circuit protection, over-voltage protection, and emergency shut-off. In the event of a fault condition, the heater control PCB also sends a feedback signal to the PLC, which activates appropriate fault alarms and safety mechanisms.
Output Indications
Heater control cards commonly include LED indicators that provide visual feedback on system status, communication activity, and alarm conditions. In more advanced systems, real-time temperature monitoring is achieved by transmitting temperature data to a Human-Machine Interface (HMI).
Design of Heater Control Cards
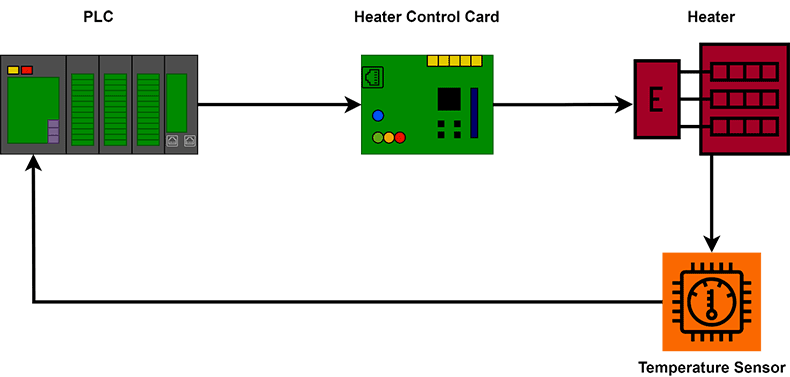
Industrial heater control system
The design of a heater control card/PCB depends largely on the application requirements. Various design methodologies and power switching components are used based on the load type and control strategy.
The power section and thermal management are two critical aspects in the PLC heater control PCB design:
Power section
The power section of a PLC heater control PCB uses power semiconductor devices, such as TRIACs, IGBTs, or power MOSFETs.
TRIACs are commonly used in low-cost applications for switching AC resistive loads, typically with a phase-angle control circuit. MOSFETs are suitable for low to medium voltage applications that require fast switching.
For high-voltage or high-current applications, IGBTs are preferred due to their superior power-handling capability. However, the switching speed of IGBTs is moderate at best. They are frequently used in PWM (Pulse Width Modulation)-based temperature control circuits.
Solid-state relays are another solid option for switching AC and DC loads in heater control applications.
Thermal management
Thermal management is another important aspect of the heater control card circuit design.
High-power switching components like TRIACs, MOSFETs, and IGBTs generate excessive heat that can easily damage the circuit board and its components.
Therefore, both active and passive heat dissipation strategies are used, such as cooling fans and heat sinks.
The sizing of heat sinks is based on thermal resistance, ambient temperature, and power dissipation. In space-constrained PCBs, thermal vias or copper planes are used for enhancing heat transfer and improving thermal performance.
For the PCB, the circuit design must comply with IPC-2221 standards regarding copper thickness and trace width.
Copper thickness should be 2 oz or higher for high-current traces.
Additionally, galvanic isolation is provided using optocouplers to separate the low-voltage control and high-voltage power circuits.
Other protection features of the heater control PCB circuit include EMI filters, snubber circuits, fuses, MOVs, free-wheeling diodes, and star grounding.
Applications of PLC Heater Control
PLC-controlled heating systems are used in a wide range of industries, including plastics, HVAC, food processing, textiles, and pharmaceuticals. Precise temperature control is critical for the quality control and production process in these industries.
Some notable applications of PLC-controlled heater cards in industries are:
- Temperature control of industrial ovens and furnaces
- Die temperature regulation in plastic extrusion machines
- Temperature control of chemical reactors
- Temperature control of industrial steam boilers
- Temperature control of pasteurizers in the food processing industry
- Temperature regulation of reheating coils in HVAC systems
- Temperature regulation of sealing jaws in packing machines
Turnkey PCBA Manufacturer with R&D Capabilities for PLC Industrial Control
Heating is a crucial part of many industrial processes. Accurate and precise temperature control is essential for producing high-quality products and maintaining a safe working environment. How do you ensure your PLC heating control project works and yields satisfactory results?
ou can work with the EMS (electronic manufacturing service) PCBA manufacturer, PCBONLINE, to develop your industrial control project and have the PLC controllers and heater control cards manufactured and tested under one roof. It has:
- Two large advanced PCB manufacturing bases for industrial control PCBs,
- One turnkey PCB assembly factory for PLC PCB assembly and box-build assembly,
- Stable material supply chains and strategic cooperation with the mainstream MCU manufacturers for all electronic components,
- Long-term cooperation with the top 3 mold and enclosure manufacturers in China for jigs/textures, molds, and enclosures.
- An R&D team and professional CAM engineers for project development and DFM (design for manufacturing).
PCBONLINE offers free DFM before and during PLC heater control PCB prototyping/sampling to ensure the success of batch production, including checks of Gerber and BOM, jig/fixture/PCB stencil design, manufacturing process, and testing designs, and solving all issues throughout the project to ensure seamless manufacturing.
PCBONLINE can provide or assist R&D for your industrial PLC control project, including hardware and software R&D, schematics, PCB design, testing design, and enclosure design.
Completing industrial PLC heater EMS custom meeting your demands, including PCB manufacturing, component sourcing, PCB assembly, PCBA value-added and testing/inspections in the post-assembly stage, enclosures, and box-build assembly.
PCBONLINE has rich experience in thermal management for industrial controls, and both active and passive heat dissipation strategies are employed.
PLC projects prioritize thermal management and high-current carrying capabilities. For this, we have advantages in thermal management with thermal path design, PCB busbars, thick-copper PCBs up to 14oz, copper-core PCBs, and ceramic PCBs, etc.
High-quality PLC control PCB/PCBA manufacturing meeting your application demands, including ISO 9001:2015, ISO 14001:2015, IATF 16949:2016, RoHS, REACH, UL, IPC-A-610 Class 2/3, and IPC-A-610 Class 2/3.
No matter what quantity you want, we always prioritize quality and provide service and support that meet and exceed your expectations.
PCBONLINE has rich R&D and EMS manufacturing experience in industrial PLC projects, such as PLC heater control cards. You can send your R&D and manufacturing requests to PCBONLINE. To get a quote for your PLC industrial control project, please email info@pcbonline.com.
Conclusion
PLC heater control PCBs serve as an essential component of modern industrial temperature control systems. PLC heater control PCBs are widely used in industrial ovens, furnaces, injection molding machines, thermoforming machines, chemical reactors, steam boilers, and air handling units. To have your PLC heater control PCB manufactured with reliability and cost-effectiveness, work with the EMS industrial control PCBA manufacturer PCBONLINE.
PCB assembly at PCBONLINE.pdf