Lithium battery technology is the core of electric vehicle (EV) and hybrid electric vehicle (HEV) fabrication, and flexible PCB is a necessary component for lithium battery systems. This blog gives an introduction to lithium batteries and flexible PCBs, and you can find out how to make lithium battery packs using flexible PCBs. Let's dive in!
Part 1: What is Lithium Battery for EV and HEV
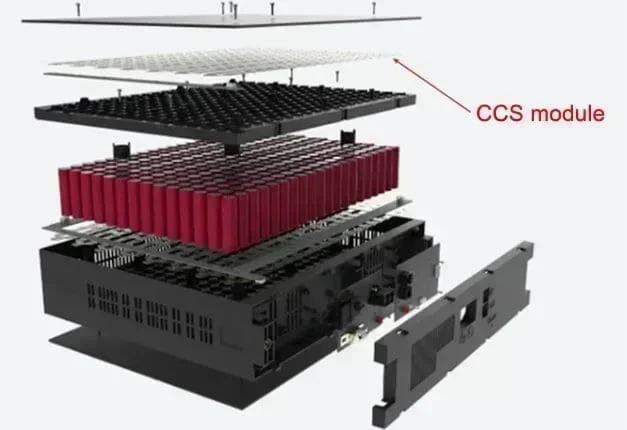
Lithium battery, also called lithium-ion battery, is the power source of EVs and HEVs. The lithium battery pack structure is pack > module > cell. Cells can be 18650 and blade battery cells, module means cell contact system, and the pack is the entire battery pack including the mechanical support and enclosure.
The battery cells are controlled by the battery management system (BMS) to charge or discharge.
The cell contact system (CCS) monitors the states ( temperatures and power) of the battery cells and transfers the signals to the BMS.
Components such as connectors, fuse, negative temperature coefficient (NTC) resistor, and busbars mount and laminate on the CCS module.
The lithium battery cells are arranged in rows and lines in the battery pack. The higher the mass density of the battery cells, the more electricity that the battery can store.
The development of the battery cells for EVs and HEVs is lead-acid battery > ternary lithium battery > lithium iron phosphate battery > sodium-ion battery.
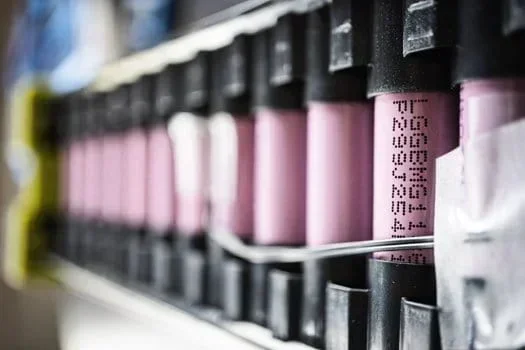
Currently, sodium batteries are still in the laboratory stage, and the mass-produced batteries are lithium batteries, including the 18650 thin-film lithium batteries and lithium solid-state batteries.
In the lithium battery pack for EVs and HEVs, printed circuit boards (PCB) including flexible PCB and FR4 PCB are used.
PCBs Used in Lithium Battery
FR4 PCB is used in the BMS.
While the cover of the lithium battery pack uses flexible PCBs (also called flexible printed circuits or FPC) because the cover space is compact.
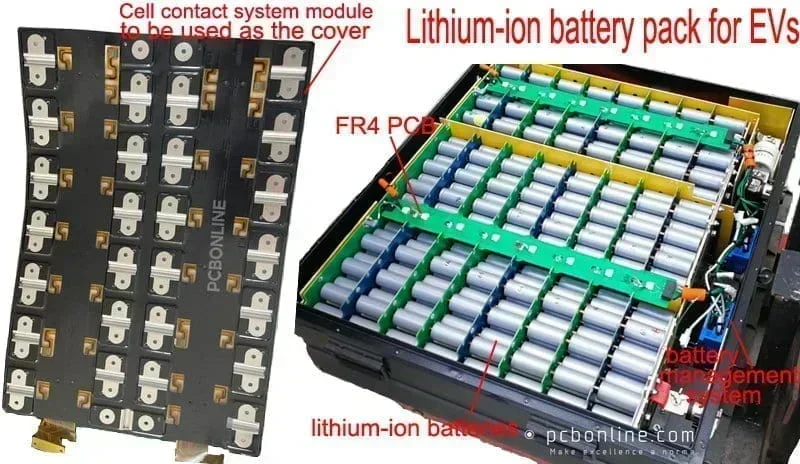
In some CCS solutions, the CCS module uses the FR4 PCB, busbars, metal connections, and black films.
In soft-pack lithium batteries, flexible PCBs are used both in the CCS module. The CCS module consists of flexible PCBA, busbars, and black films.
Part 2: What is Flexible PCB (FPC)
A flexible printed circuit board is a polyimide (PI) or polyester (PET) based circuit board, which is thin, light, and can dimensionally bend.
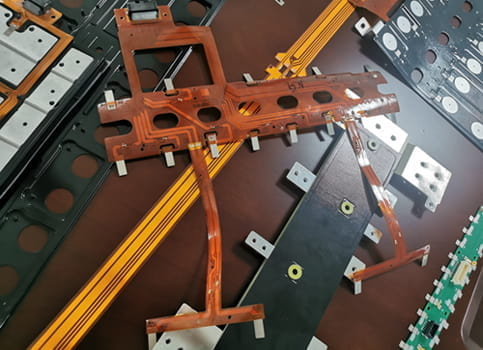
Structure of Flexible PCB
An FPC comprises the PI or PET film, copper, and adhesive.
The PI and PET films have a small dielectric constant, high electrical insulation, Tg of 80℃, and good tension resistance.
For flexible PCBs used for the cell contact system of a baterry pack, their flexible copper-clad laminate should use rolled annealled copper and adhesive.
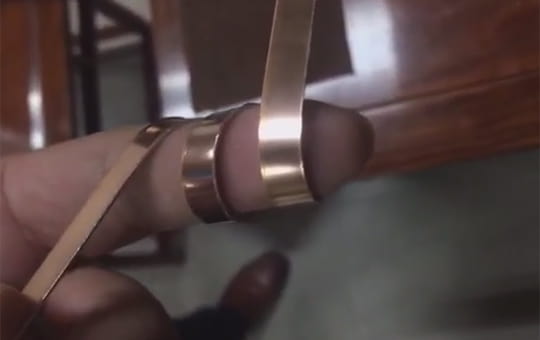
FPC using RA copper is used for dynamic applications, such as car door handles, while FPC using ED copper is used for static applications, such as car tail lights.
The adhesive in the flexible PCB is used to bond the PI or PET film and cooper. On the surface of the flexible PCB is the coverlay, which consists of an adhesive layer and a PI or PET film.
Grounding of Flexible PCB
Flexible PCBs find applications in aerospace, automotive, medical, communication, computing, and consumer electronics.
In applications, typically, flexible PCBs need grounding.
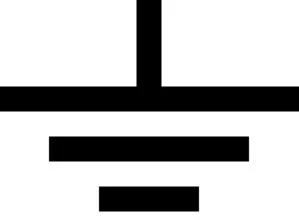
Grounding means electrically connecting the negative pole of the power supply on the FPC to the metal enclosure. This way, the metal enclosure can shield interference waves to and from the external environments.
Flexible PCBs are also grounded in the lithium battery pack of EV and HEV.
Applications of Flexible PCBs in Lithium Battery
In a lithium battery pack for EVs and HEVs, the applications of flexible PCBs include:
- The acquisition line of the BMS system, and the flexible PCB monitor the voltage and temperature of the battery cell
- The cell contact system module using the flexible PCB is responsible for signal acquisition and transmission and overcurrent protection
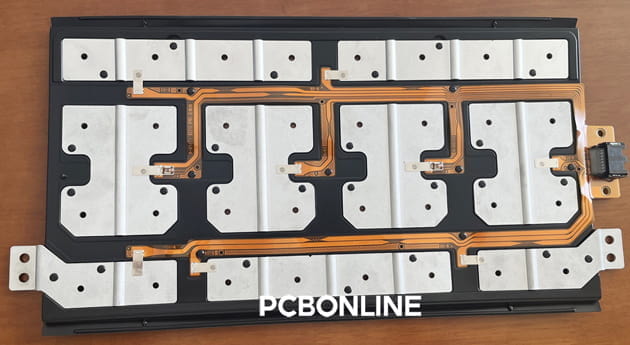
In lithium battery solutions for EVs and HEVs, FPC gradually exceeds traditional wiring hardness in use.
In the lithium battery system of an EV or HEV, about 7 to 12 flexible PCBs are being used in the CCS modules.
Advantages of Using Flexible PCBs in Lithium Battery
Using flexible PCBs in the cell contact system module to replace the traditional wiring hardness, there are advantages such as:
- High integrity. The embedded fuse, connector, NTC resistor, and busbars are assembled on the CCS module. This way, the component assembly and conductor connection become one.
- Automatic production. By using FPC, the CCS module fabrication complexity gets lower, and the CCS assembly is automated, fast, and accurate.
- Flexibility. The FPC of the CCS module allows smaller and higher-density installations and 3-D space wiring, and the appearance can change according to space constraints. In the circuit areas, the CCS module can bend to 90°and fit 180°installation.
- Lightweight. Compared with the wiring hardness solution, by using the CCS module with FPC, 1 kilogram of weight is reduced for the EV and HEV.
- Safety. In the CCS module using FPC, fuse protection current design is added. The fuse is embedded in the CCS module, which makes sure the circuit breaks when the worst condition - short circuits happens, and the battery cells won't burn or explode.
Part 3: How to Make Lithium Battery Pack using Flexible PCB
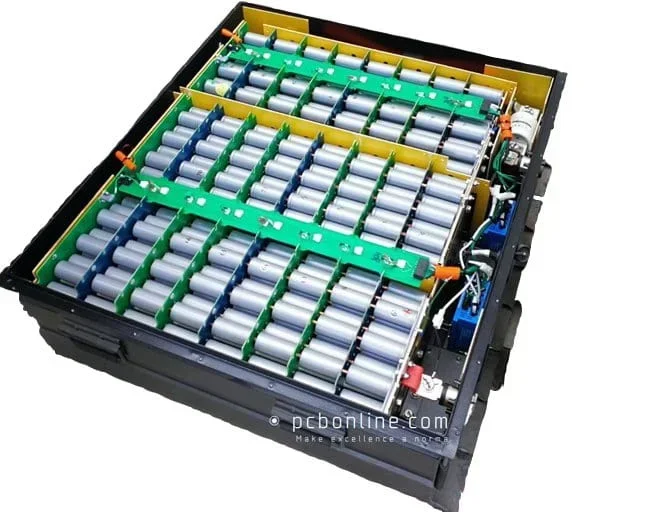
Lithium batteries for EVs and HEVs are custom-designed and fabricated. The fabrication of lithium batteries can be divided into three parts: battery cell sourcing, cell contact system assembly, and battery pack assembly.
You can purchase lithium battery cells such as the 18650 battery from the battery manufacturer BYD's FinDreams Battery and the blade battery from Contemporary Amperex Technology Co. Limited.
You can arrange the array of battery cells according to the power and space requirements of the EV or HEV.
You need to design the flexible PCB and the cell contact system module according to the array of battery cells and the power requirements of the battery.
The lithium battery pack assembly is automatic. The mechanical arms pick and place the CCS module on the battery cells and install the mechanical enclosure onto the battery pack.
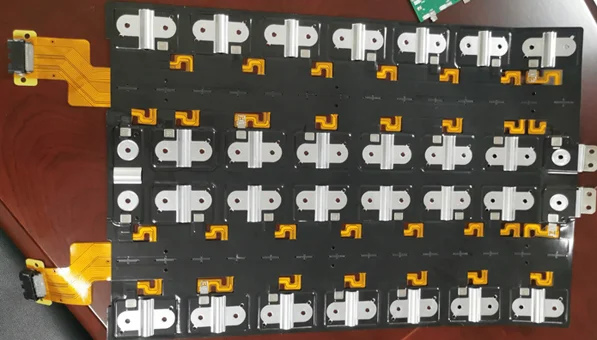
In regards to the CCS assembly, you can check the CCS assembly video below. And we will reveal the process step-by-step.
- Step 1. Flexible Copper Clad Laminate (FCCL) Fabrication
- Step 2. Cut Laminate
- Step 3. Flexible PCB Circuit Generation
- Step 4. Surface Finish
- Step 5. AOI
- Step 6. Cut and Attach FPC Coverlay
- Step 7. Flexible PCB Lamination
- Step 8. Silkscreen
- Step 9. Electrical Testing
- Step 10. Flexible PCB Assembly
- Step 11. Flexible PCBA testing
- Step 12. CCS Lamination/Assembly
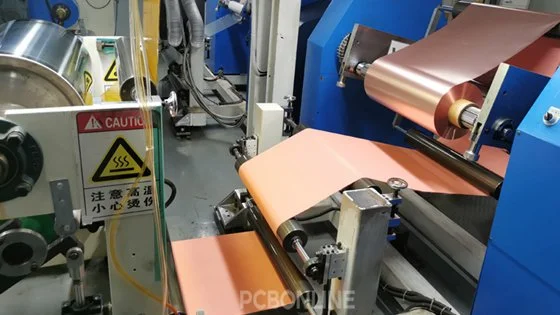
From the one-stop flexible PCB manufacturer PCBONLINE, FCCL is fabricated by laminating the copper foil, adhesive, and PI films. Meanwhile, the coverlay is also fabricated by thermally laminating the PI film and adhesive.
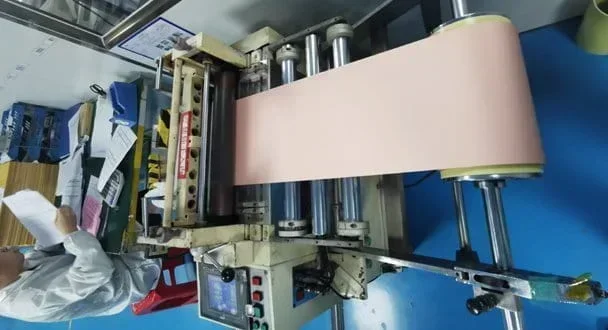
At PCBONLINE, the FCCL is cleaned, laminated, and rolled in the toll-to-toll way. Then the FCCL is cut to be the required size.
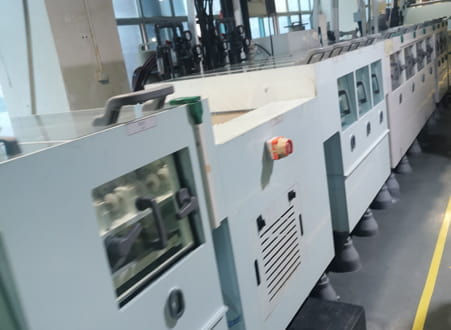
The FCCL is exposed with circuits and etched to generate the circuit images. Later, the copper laminates are scrubbed, cleaned, and dried.
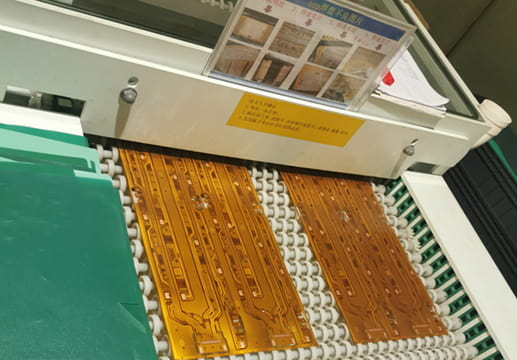
The typical surface finish for flexible PCBs can be OSP or immersion gold. The above image shows an OSP surface finish line specialized for flexible PCBs.
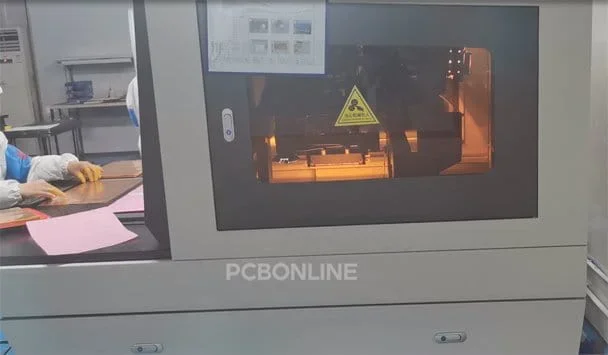
After the circuit generation, the flexible PCB manufacturer has an automatic optical inspection to make sure the circuit is okay.
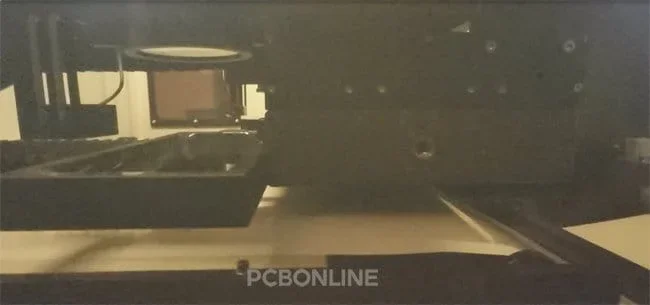
In a machine, the coverlay is automatically cut to the required size. And then, in another machine, the coverlay is drilled and attached to the flex PCB.
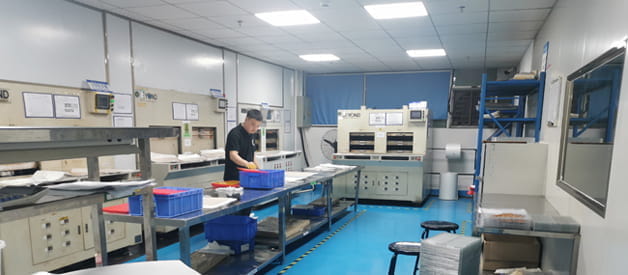
After attaching the coverlay to the flexible PCB, the FPC manufacturer thermally laminates the circuit boards so that the coverlay and PCB layers form a reliable circuit board.
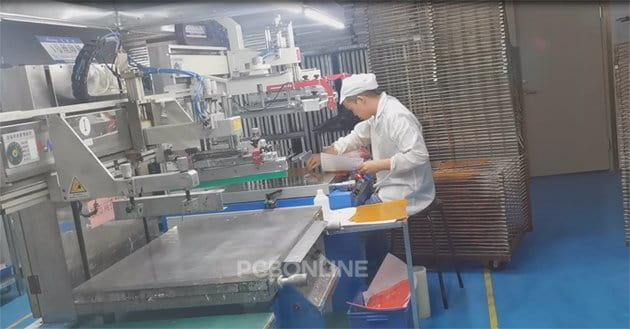
At this step, the silkscreen (symbols and marks) is printed on the surface of the flexible PCB.
This is the second time for AOI circuit testing with a jig specialized for the flex PCBs.
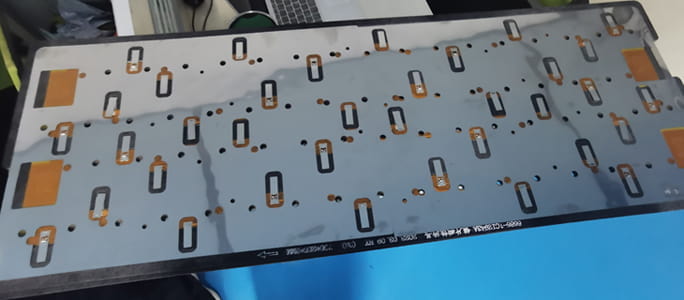
At this step, the one-stop FPC manufacturer PCBONLINE uses a specialized stainless steel jig to fix the flexible PCB and place it on the SMT line.
In the PCBA manufacturing process, the connector, NTC resistor, fuse, and small nickel sheets for connection are surface mounted on the flexible PCB.
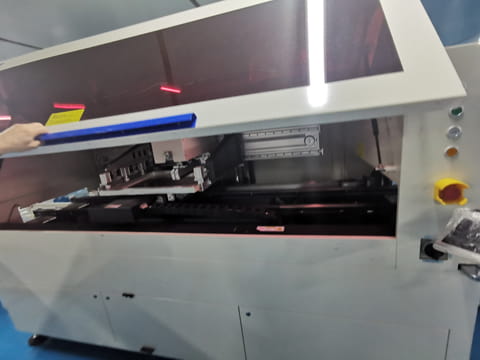
Then the flexible PCBA is reflow soldered to be the finished flex PCBA.

At PCBONLINE, there is full testing equipment to ensure the good quality and functions of the flexible PCB assemblies.
The tests include tension test, bending test, button strike life test, hand sweat test, environmental protection test, metallographic microscope inspection, fuse test, bridge test, DC resistance test, withstand voltage test, impedance test, and salt spray test.
A CCS module consists of an FPC PCBA, busbars, and black films.
PCBONLINE has two methods for CCS assembly according to your design requirements. One is thermal lamination, and the other is the blister heat riveting method.
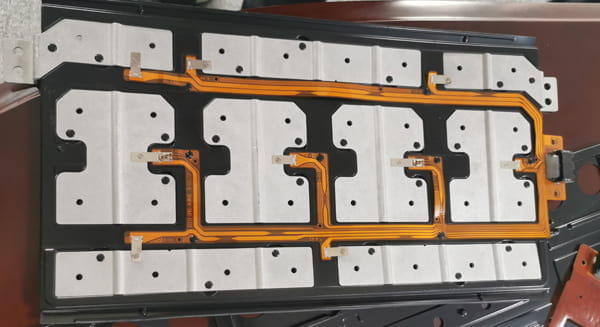
The aluminum busbars are laser soldered in series and parallels in advance.
The CCS manufacturer PCBONLINE laminates the flexible PCBA, black films, and busbars to make the CCS module, and the fuse on the PCBA is embedded in the module.
Part 4: One-Stop FPC and CCS Assembly Manufacturer for Lithium Battery
PCBONLINE is a one-stop flexible PCB and CCS module manufacturer in Shenzhen, China. It is an ISO and IATF-certified source factory manufacturer with two large PCB manufacturing bases and one PCB assembly factory.
PCBONLINE provides CCS assembly from A to Z, including flexible copper-clad laminate fabrication, flexible PCB fabrication, flexible PCB assembly, FPC assembly testing, and CCS module assembly.
Here are the advantages of PCBONLINE in FPC and CCS modules for lithium batteries for EVs and HEVs:
- Expertise - you can hand over all the CCS projects to PCBONLINE without the need for drawing and wiring.
- PCBONLINE provides all-in-one services, including FPC, nickel sheets, busbars, and CCS assembly, and guarantees quality and in-time delivery.
- PCBONLINE adopts the toll-to-toll process for flexible PCB fabrication, which increases efficiency and production yield.
- The maximum length of FPC in the CCS module of mass production is 1.8m.
- PCBONLINE can collaborate with you on R&D for your lithium battery system for EVs and HEVs.
- PCBONLINE's FPC and CCS assembly for lithium batteries are IATF 16949 and ISO 9000 certified.
PCBONLINE has rich manufacturing experience in FPC assembly and cell contact system module assembly for lithium batteries. If you want CCS modules for lithium batteries, you can send your request to info@pcbonline.com. PCBONLNE will offer one-on-one engineering support and customer services throughout your lithium battery project.
Conclusion
This blog introduces lithium batteries and flexible PCBs respectively and how to fabricate lithium batteries using flexible PCBs. A lithium battery for EVs and HEVs has the structure in the pack > module > cells level, and the cells contact system module is important for lithium battery fabrication. The flexible PCB in the CCS modules is used in the lithium battery to connect and monitor the battery cells and transmit signals. If you want to work with a one-stop flexible PCB and CCS module manufacturer for lithium batteries, the source factory manufacturer PCBONLINE won't let you down.
Battery Management System Manufacturing at PCBONLINE.pdf
CCS Product Introduction - PCBONLINE.pdf
© This article is an original work of the PCBONLINE team. Please indicate the author PCBONLINE if you reprint. If the article is reproduced without permission or indicating the author's source, PCBONLINE reserves the right to investigate the infringement.