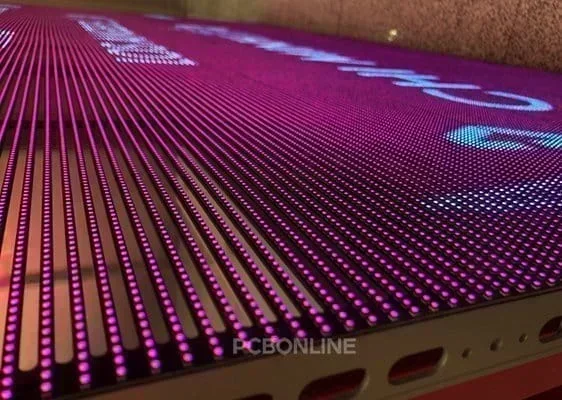
In the developing electronics industry, LED light boards are among the important applications of PCBs. LED light PCBs are very common and are found almost everywhere in lighting. In this article, we will delve into LED light PCB boards, understanding their types and designing and manufacturing process!
In this article:
Part 1: What is an LED Light PCB? Part 2: Types of LED Light PCBs Part 3: Assembly Methods for LED PCBs Part 4: Steps Involved in Making Your LED PCB Part 5: Key Design Considerations When Making an LED PCB Part 6: One-stop LED Light PCB Manufacturer and AssemblerWhat is an LED Light PCB?
We will begin by understanding the LED. LED is the short form of "Light-Emitting Diode", it is simply a semiconductor device that emits light when an electronic current passes through it. Similarly, an LED PCB refers to a specialized Printed Circuit Board (PCB) designed for LED applications. It is important to understand that for an LED, emitting light also produces heat as a result. Therefore, an important specification for LED PCBs is that they should have an effective heat dissipation mechanism.
The Applications of LED PCBs
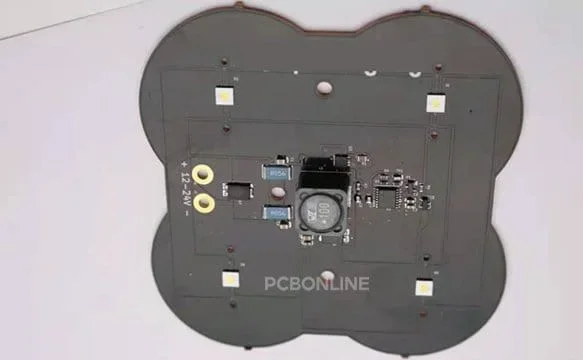
398W/mK 8-layer copper-based LED PCB for automotive front light
LED light PCB boards are crucial for connecting and managing LED components for modern lighting products. The use of LED PCBs is wide across a range of applications, such as:
- Street and tunnel lighting applications
- Indoor and outdoor lighting solutions
- LED traffic light systems
- Solar-powered LED lighting systems
- Offshore ship lighting and underwater lighting
- Stage lighting and photography lighting
The applications of LED light boards are not limited to the above fields as LED light technology keeps evolving.
Advantages of LED PCBs
LED PCBs offer several key benefits including energy efficiency, compactness, and longevity.
Energy efficiency: LED PCB boards consume significantly less power, making them a cost-effective lighting option.
Longevity: The high-quality PCBs enable high-lumen LED lights to last over 25,000 hours. They require far fewer replacements than traditional bulbs.
Compact design: Due to the small form factor of LED PCBs, they are suitable for compact and intricate designs.
Types of LED Light PCBs
LED boards come in different types offering different advantages. In this section, we will discuss these types of LED PCBs so that you can choose what fits best for your application.
Aluminum PCB
Aluminum-based PCBs are common for LED lights because of their cheap prices and good thermal conductivity. Aluminum PCBs and copper-based PCBs are known as metal-core PCBs, which typically feature a thermal conductivity ranging from 1W/m.K to 8W/m.K (Copper PCBs are better than aluminum PCBs in thermal dissipation).
FR4 PCBs
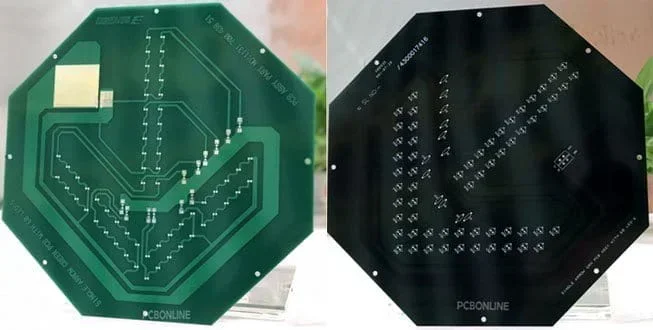
FR-4 PCBs are lightweight and suitable for low-power LED applications where insulation is prioritized. FR-4 stands for "flame retardant level 4". This epoxy laminate material has high electrical insulation properties. The thermal conductivity of FR4 PCBs is about 0.3W/m.K. For LED lights, FR4 PCBs provide stability and light weight.
Copper-based PCBs
Another option for LED lights is copper-based PCBs. The ceramic material can be aluminum nitride or aluminum oxide. These boards are designed for superior electrical conductivity and thermal management. If the requirement of the LED PCB is high current where heat dissipation is critical, copper-based PCBs are an optimal option. Their thermal conductivity ranges from 1W/m.K to 398W/m.K, with the PCB layers from 1 to 8.
Ceramic LED PCBs
Ceramic PCBs can be utilized for high-intensity LED lights in industrial or automotive settings. They offer excellent thermal conductivity and electrical insulation. Their thermal properties make them suitable for high-power LED applications that require fast heat dissipation. These LED PCBs are also durable and can withstand high temperatures, chemicals, vibrations, etc.
Flexible LED PCBs
Flexible LED PCB boards, made of PI (polyimide) or PET (polyester), are bendable and flexible. They are ideal for LED strips and unique lighting solutions, such as transparent flexible LED lights. Additionally, flexible PCBs maintain excellent performance even under extreme conditions, which makes them suitable for automotive and outdoor applications.
Assembly Methods for LED PCBs
LED light boards can be assembled using any of the two commonly available methods, Surface Mount Assembly and Thru-hole Assembly. Let's discuss more about these assembly techniques:
Surface-mount assembly (SMT)
In SMT assembly, components are mounted directly on the PCB surface, allowing for dense and complex circuitry. This type of assembly is possible for Surface Mount Devices (SMD) that are made to solder on top of the board and are relatively smaller than their through-hole counterparts.
SMT is the standard assembly method for LED boards due to its flexibility in handling multiple components efficiently. The above image illustrates an SMT-based LED PCB board that comprises a number of SMD LEDs.
Chip-on-board assembly (COB)
The chip-on-board assembly is done by inserting the components through holes available in the PCB. It includes two methods — wire bonding COB and flip-chip COB. It integrates the LED chips on the PCB, providing much better lighting quality and heat dissipation.
Wire bonding uses gold wires to connect the LED die and the PCB. The electrodes and wires are on the light-emitting side, so they can affect the lighting quality to some degree.
Flip-chip COB LED flips the light source over and installs it with the front side facing down. It can withstand higher drive currents and provides higher light density. Flip-chip COB is getting more and more popular due to its excellent light uniformity, color consistency, and thermal dissipation.
Both of the above-described assembly techniques are used in LED light PCB assembly. But when it comes to mid to high-end applications, COB assembly stands out as it ensures higher lumen, more light uniformity, and excellent thermal dissipation.
Steps Involved in Making Your LED PCB
Following are the common steps you will need to follow to create your LED board.
Designing your LED PCB
Creating an LED PCB starts with thorough planning and design. Begin by defining the specifications of your project, such as the number of LEDs, their arrangement, power requirements, and any extra features. Use PCB design software like AutoCAD, Altium, Proteus, etc, to develop a detailed schematic of your LED circuit.
Creating the PCB Layout
Place and connect all components accurately to generate a layout for PCB fabrication. Next, convert your schematic into a physical layout using PCB design software. This step involves strategically placing the LED chips, additional components, and copper traces on the board. Don't forget to follow the best practices for effective thermal management and signal integrity.
Choosing the right materials
Once the design is done, the next task is to determine the material of the board. So, choose a suitable substrate like FR4 fiberglass, aluminum, ceramic, etc. Additionally, consider the thickness and copper weight of the PCB, matching it to the power and performance needs of your project. Aluminum PCBs are layered with a thermally conductive dielectric material that rapidly transfers heat, supporting efficient, long-lasting LED performance. Traditional PCBs struggle with heat dissipation, but metal-core PCBs (MCPCBs), particularly those made of aluminum, handle this demand remarkably well.
Manufacturing and assembling the LED PCB
It's time to move to the manufacturing part.
In case the LED application you are working on is relatively complex or needs a larger-scale production, approaching to professional manufacturing services such as the LED PCB manufacturer PCBONLINE is recommended. Choosing the right manufacturer can make all the difference for your project. The PCB manufacturers use advanced processes, such as photolithography and precise etching, to create high-quality PCBs with precision and efficiency in no time. Industry leaders like PCBONLINE offer both surface-mount and thru-hole assembly options, providing reliable and high-performance PCB assemblies.
With your LED PCB board ready, the PCB manufacturers mount the components on the PCB. The assembly methods include SMT assembly and COB assembly. You can view the detailed SMT manufacturing process and COB manufacturing process from PCBONLINE's previous blogs.
Key Design Considerations When Making an LED PCB
For LED PCBs to perform at their best, several key design factors need attention.
Thermal management
Effective heat dissipation is essential for sustaining LED performance and longevity. Using metal-core PCBs, or incorporating heat sinks can significantly reduce thermal buildup and prevent overheating.
Current control
Precise control of current is vital to maintain consistent brightness and avoid LED burnout. Current-limiting resistors or constant-current drivers are commonly used to ensure stable and accurate current flow through the LEDs.
Component placement
Component placement is important. Thoughtful placement of LEDs and other components on the PCB optimize light distribution and enhance the uniformity of illumination.
Layout optimization
An optimized PCB layout is crucial for maintaining signal integrity and minimizing electromagnetic interference (EMI). To optimize the layout, careful design of signal traces, ground planes, and power routing contributes to reliable performance.
These considerations are essential in creating high-performing, durable LED PCBs suitable for a range of applications.
One-stop LED Light PCB Manufacturer and Assembler
If you want PCB fabrication and manufacturing for your LED application, work with the high-quality LED PCB manufacturer PCBONLINE which provides one-stop electronic manufacturing services, including prototypes/samples, R&D, PCB fabrication, component sourcing, PCB assembly, PCBA value-added, and LED light box-build assembly.
Founded in 1999, PCBONLINE has two large advanced PCB manufacturing bases, one EMS PCB assembly factory, stable supply chains, and an R&D team.
PCBONLINE manufactures all types of LED light PCBs that meet your custom demand, including aluminum PCBs, copper-based PCBs, ceramic PCBs, FR4 PCBs, and flexible LED PCBs.
Strong LED light assembly capabilities. Both SMT assembly and COB (wire bonding and flip-chip) are available.
PCBONLINE offers one-on-one engineering support and free design for manufacturing (DFM) and will solve all technical issues to ensure a smooth and successful production ready for bulk manufacturing.
As a source factory manufacturer, the LED light PCBs and PCBAs from PCBONLINE are cost-effective with a 98% in-time delivery rate.
High-quality LED light PCB manufacturing certified with ISO 9001:2015, ISO 14001:2915, IATF 16949:2016, RoHS, REACH, UL, and IPC-A-600 Class 2/3.
To get a quote for one-stop LED light PCB manufacturing, please contact info@pcbonline.com. No matter what quantity of LED light boards you want, PCBONLINE can work for you with high quality and reliability.
Conclusion
LED light PCBs transform how we illuminate our world. By understanding the types of LED PCBs and considerations in their design and manufacturing, you can make the right choice for any innovative and modern lighting solutions. To get one-stop LED light PCB fabrication and assembly until you receive the finished LED lighting products that have been tested to work successfully, work with the high-quality LED light PCB manufacturer PCBONLINE.
PCB fabrication at PCBONLINE.pdf