PCBA integrates SMT (precision surface mounting) and THT (durable through-hole connections) for hybrid designs. Core soldering techniques: reflow (SMT mass production), wave (THT), thermocompression (micro-interconnects), and manual (prototyping/repairs). Rigorous AOI/X-ray inspections ensure quality across automotive, medical, and consumer electronics, balancing efficiency, reliability, and scalability for custom or high-volume needs.
In this article:
Part 1. What is PCB Assembly and Soldering Services? Part 2. PCB Assembly Service Core Process Part 3. Four Major Soldering Technology DetailsWhat is PCB Assembly and Soldering Services?
PCB Assembly (PCBA)
PCBA is the process of mounting electronic components onto a PCB using automated methods like SMT (for tiny parts) and THT (for bulkier components). It includes steps like solder paste application, precision placement, soldering (reflow/wave), and rigorous testing to ensure a fully functional board for industries like consumer tech, automotive, or medical devices.
Soldering Services
Soldering services create electrical connections on PCBs via techniques like reflow (SMT), wave (THT), or hand soldering for prototypes. Advanced options include selective soldering and post-process inspections (X-ray, thermal tests) to guarantee reliability in mass production, small batches, or repairs.
PCB Assembly Service Core Process
Surface Mount Technology (SMT)
1.Solder Paste Application (Stencil Printing)
The SMT process begins with solder paste application using a stencil printer. A stainless steel stencil, laser-cut to match the PCB’s pad layout, is aligned over the board. Solder paste (a mixture of tiny metal alloy particles and flux) is dispensed onto the stencil and spread evenly by a squeegee blade. The paste transfers through the stencil apertures onto the PCB pads. Precise control of pressure, speed, and stencil alignment ensures consistent paste volume, critical for reliable solder joints later.
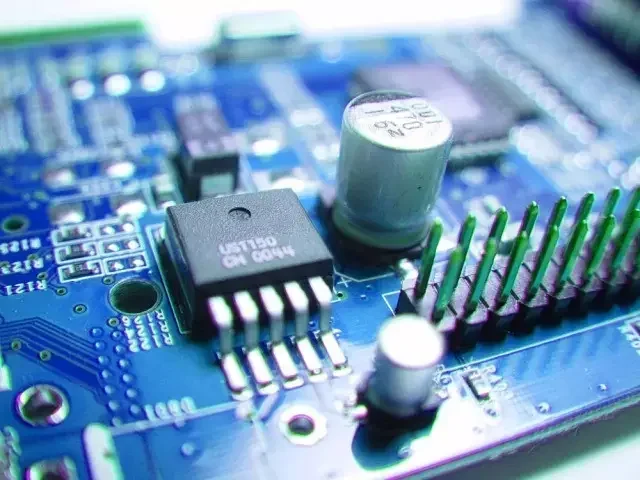
2.Component Placement (Pick-and-Place)
Next, a pick-and-place machine mounts components onto the solder paste-covered pads. Using vacuum nozzles or grippers, the machine picks components from reels, trays, or feeders and positions them at high speed with micron-level accuracy. Vision systems align fiducial marks on the PCB and components to correct placement offsets. Tiny passive components (e.g., 01005 resistors) and large ICs (e.g., BGAs) are placed sequentially, often at rates of 20,000–100,000 components per hour.
3.Reflow Soldering
After placement, the PCB enters a reflow oven, where it passes through multiple temperature zones:
Preheat: Gradual heating (1–3°C/sec) to activate flux and evaporate solvents.
Soak: Stabilization (~60–120 sec) to minimize thermal shock and remove oxides.
Reflow: Peak temperatures (typically 220–250°C) melt the solder paste, forming metallurgical bonds. For lead-free alloys (e.g., SAC305), this zone lasts 30–60 sec above 217°C.
Cooling: Controlled solidification to prevent brittle joints or component damage.
Convection, infrared, or vapor phase heating ensures even heat distribution across the board.
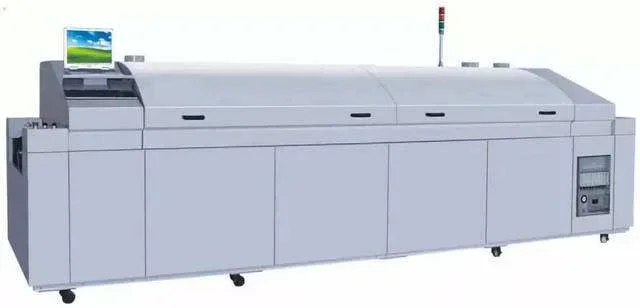
4.Inspection and Quality Control
Post-reflow, automated inspection verifies quality:
- AOI (Automated Optical Inspection): Cameras check for misalignment, tombstoning, or solder defects (bridges, insufficient paste).
- SPI (Solder Paste Inspection): 3D scanners measure paste volume/height pre-reflow to prevent defects.
- X-ray Inspection: For hidden joints (e.g., BGA, QFN), X-rays detect voids, cracks, or poor wetting. Defective boards are flagged for rework (e.g., solder touch-up or component replacement).
Through-hole technology (THT)
Through-hole technology (THT) is a traditional PCB assembly method where components with long leads are inserted into pre-drilled holes on the board and soldered to pads on the opposite side. This technology provides strong mechanical bonds, making it ideal for high-reliability applications, large components, or parts subject to mechanical stress. THT involves several key steps: drilling holes, inserting component leads, wave soldering (or hand soldering), and trimming excess leads. While largely supplanted by surface-mount technology (SMT) for miniaturization, THT remains essential for connectors, transformers, electrolytic capacitors, and other components requiring robust physical connections. The process is more labor-intensive than SMT but offers easier prototyping, better thermal performance, and higher durability in harsh environments.
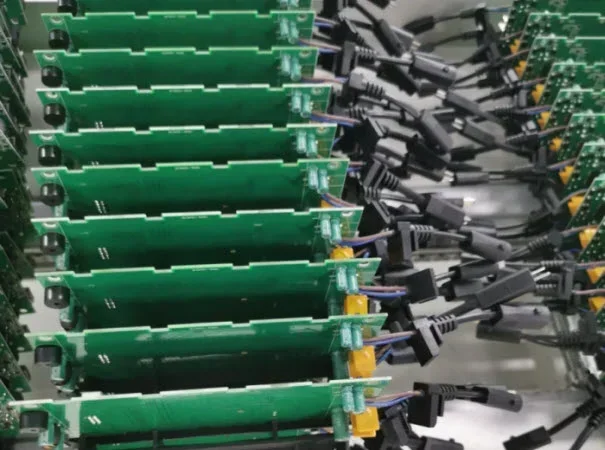
Mixed Technology (SMT+THT)
Mixed technology in PCB manufacturing combines Surface Mount Technology (SMT) and Through-Hole Technology (THT) to leverage the advantages of both methods. SMT components are mounted directly onto the PCB surface, allowing for high-density, automated assembly with smaller footprints. THT components, on the other hand, are inserted into drilled holes and soldered for stronger mechanical bonds, making them ideal for high-power or high-reliability applications.
The assembly process typically involves SMT placement first, where pick-and-place machines position SMDs (Surface Mount Devices) followed by reflow soldering. THT components are then inserted, either manually or via automated insertion machines, and secured using wave soldering or selective soldering. This hybrid approach ensures optimal performance, durability, and flexibility in complex PCB designs.
Challenges include managing thermal profiles during soldering (to prevent damage to SMT parts) and ensuring proper component spacing. However, mixed technology remains essential for modern electronics, balancing miniaturization with robustness in applications like automotive, industrial, and aerospace systems.
Four Major Soldering Technology Details
Reflow Soldering
Reflow soldering uses a precisely controlled temperature profile (preheating, soaking, reflow, cooling) to melt and solidify solder paste, making it the primary method for assembling SMT components. Its advantages include high-temperature precision (±2°C tolerance) and mass-production efficiency, ideal for micro-sized SMT components in consumer electronics like smartphones and laptops. This technology requires strict solder paste printing quality control, supported by stencil printers and SPI (Solder Paste Inspection) systems. It is best suited for high-density PCBs dominated by SMT, such as 5G modules and IoT sensors, but lacks compatibility with through-hole (THT) components.
Wave Soldering
Wave soldering immerses PCBs in a molten solder "wave" to batch-solder through-hole components (e.g., connectors, relays), commonly used in automotive electronics and home appliance control boards. Its strengths lie in high throughput and cost-effectiveness, though thermal stress may cause PCB warping or solder bridging (especially for fine-pitch components). Mitigation strategies include fixture clamping and nitrogen atmosphere protection. Typical applications include industrial power modules and LED driver boards requiring mechanical durability, but it is unsuitable for miniaturized SMT-focused designs.
Thermocompression Bonding (TCB)
Thermocompression bonding achieves high-density interconnects (e.g., flip-chip, silicon photonics) by applying precise pressure (50–200N) and heat (250–400°C) without solder, drastically reducing voids and misalignment defects. Its key advantage is enabling micron-level pad spacing (<50μm), making it critical for 5G base station chips, AI accelerators, and HBM (High Bandwidth Memory) stacking. Primary industries include advanced semiconductor packaging, optical transceivers, and aerospace electronics. However, TCB demands high equipment costs, complex processes, and alignment systems with sub-micron accuracy.
Manual Soldering
Manual soldering relies on operators using soldering irons for point-to-point connections, ideal for low-volume repairs, prototypes, or heat-sensitive components (e.g., temperature-critical sensors). While highly flexible for irregularly shaped parts or hybrid-process PCBs, solder joint quality depends heavily on operator skill, requiring strict ESD protection and visual/X-ray inspection. Typical use cases include custom lab instruments, medical device repairs, and small-batch military electronics. However, inconsistent output and low efficiency make it unsuitable for mass production.
PCB Assembly (PCBA) and Soldering Services involve mounting components onto circuit boards using SMT (automated, high-speed for miniaturized parts) and THT (durable connections for larger components). Mixed-technology PCBs combine both methods. Soldering techniques include reflow (SMT mass production), wave (THT bulk soldering), thermocompression (ultra-fine interconnects), and manual (prototypes/repairs). Quality is ensured via automated optical/X-ray inspections. These processes support industries from consumer electronics to aerospace, balancing precision, scalability, and adaptability for high-volume or custom needs.
One-Stop HDI PCB Manufacturer and Its PCB Via Filing Capabilities
If you're looking for turnkey HDI electronics manufacturing services (EMS) from hardware development to PCBA fabrication and box-build assembly, you can work with the one-stop HDI PCBA manufacturer PCBONLINE.
Founded in 1999, PCBONLINE has R&D capabilities for HDI projects and EMS manufacturing capabilities, including via filling for stacked vias. It provides 4-to-64-layer HDI PCB fabrication, assembly, and PCBA box-build assembly. You can order various HDI PCBs from PCBONLINE, such as FR4, polyimide (flexible PCB), polyimide + FR4 (rigid-flex PCB), and PTFE/Rogers (high-frequency PCB).
3000m² of production capacity per day for HDI PCBs with builds of 1+N+1, 2+N+2, 3+N+3,4+N+4, and arbitrary interconnection in any layers.
PCBONLINE has hardware and software R&D capabilities for IoT applications requiring HDI design, including PCBA and enclosures.
We can manufacture complex PCBs with stacker vias, via-in-pad, microvias, inlay boards, heavy copper designs, and hybrid and fine structure lay-ups.
Besides HDI PCB fabrication, we have powerful capabilities in fine-pitch assembly for HDI PCB assembly.
We have rich R&D and manufacturing experience for HDI applications such as FPGA boards.
High-quality HDI PCB and PCBA manufacturing certified with ISO 9001:2015, IATF 16949, RoHS, REACH, UL, and IPC-A-610 Class 2/3.
Here'e the PCB via filing capabilities at PCBONLINEL:
- Micriavia filling with copper: laser via size 0.1-0.125mm, priority 0.1mm
- Finished hole size for via-in-pad filling with resin: 0.1-0.9mm (drill size 0.15-1.0mm), 0.3-0.55mm normal (drill size 0.4-0.65mm)
- Max aspect ratio for via-in-pad filling with resin PCB - 12: 1
- Min resin plugged PCB thickness: 0.2mm
- Max via-filling ith resin PCB thickness: 3.2mm
- Making different hole sizes with via filling in one board: Yes
- Via filling with copper/silver: Yes
If you need HDI PCBAs or any other PCBAs requiring via filling, please send your email to PCBONLINE at info@pcbonline.com. We will provide one-on-one engineering support to you.
Conclusion
Via filling is used for creating stacked vias in HDI PCB fabrication, BGA/CSP/QFN IC packaging, and filling PCB via-in-pad with resin during multilayer PCB fabrication. If you need one-stop electronics manufacturing for your HDI PCBA project, contact the one-stop advanced PCB manufacturer PCBONLINE for high-quality PCBA and box-build solutions tailored to your project's needs.
PCB fabrication at PCBONLINE.pdf