At the core of modern electronic products, the integration of components continues to rise, which inevitably brings severe heat dissipation challenges. Traditional FR-4 circuit boards often seem to be unable to cope with thermal management. It is in this context that Metal Core PCB (MCPCB) came into being. With its excellent heat dissipation performance and stable electrical characteristics, it quickly became an ideal solution for cutting-edge fields such as high-power electronic equipment, LED lighting and automotive electronics.
In this article:
Part 1. The core structure and principle of MCPCB Part 2. Why are MCPCBs ideal for high power applications? Part 3. Application of MCPCB in various industries Part 4. MCPCB Requirements to Meet DemandsThe core structure and principle of MCPCB
MCPCB is very different from the common circuit boards we are familiar with. It no longer uses glass fiber epoxy resin (FR-4) as the substrate but uses a metal substrate as its core support. This substrate is usually made of aluminum or copper with excellent thermal conductivity. The basic structure of MCPCB is usually composed of three tightly combined layers, and each layer carries a unique and critical function. The bottom layer is the metal substrate, which is the core of the entire heat dissipation system. It can quickly conduct the heat generated by the components with amazing efficiency. It is usually aluminum-based or copper-based. Among them, aluminum substrate is the most widely used due to its excellent cost-effectiveness and thermal conductivity. Closely attached to the metal substrate is a thin and high-performance insulating layer (dielectric layer). This layer of material is crucial. It not only needs to safely isolate the circuit layer from the conductive metal substrate but also ensure that the heat can be conducted efficiently with almost no loss. Therefore, its thermal conductivity and compressive strength directly determine the overall performance of the MCPCB. The top layer is the circuit layer, which is composed of precision copper foil, responsible for carrying various electronic components and realizing complex wiring connections.
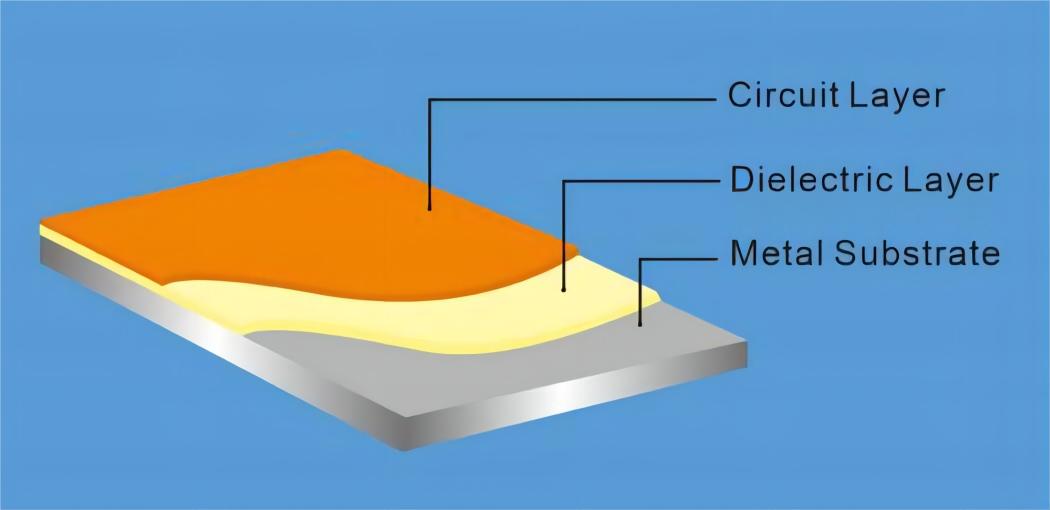
Why are MCPCBs ideal for high power applications?
The reason why MCPCB stands out among many circuit boards and is widely used in high-power scenarios is mainly due to its series of significant and irreplaceable advantages. First, and the most core advantage is its excellent heat dissipation performance. The ultra-high thermal conductivity of the metal substrate means that it can transfer the heat generated by the heating component to the external radiator or air at lightning speed, thereby significantly reducing the operating temperature of the component, which can not only effectively extend the service life of the equipment, but also greatly improve the reliability of the overall system. Secondly, thanks to its efficient heat dissipation capability, MCPCB can support higher power density, which means that in the same or smaller space, we can integrate more electronic components and carry more current, thereby achieving a more compact and higher-performance product design. In addition, due to the improvement of heat dissipation efficiency, the volume of the radiator can often be reduced, thereby reducing the size and weight of the entire product, which is especially important for modern electronic products that pursue lightness and portability. Finally, the metal substrate itself also gives MCPCB excellent mechanical stability and electromagnetic shielding capabilities, making it not easy to deform, able to adapt to more harsh working environments, and help reduce electromagnetic interference to ensure pure signal transmission.
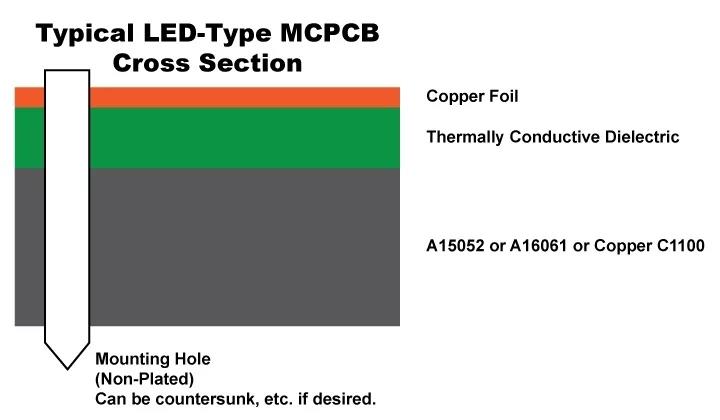
Application of MCPCB in various industries
With its unique performance advantages, MCPCB has deeply penetrated into many industries with strict requirements on heat dissipation and reliability and has become the basis for the realization of many cutting-edge technologies. In the field of LED lighting, especially high-power LED modules, which generate huge heat, MCPCB is an indispensable heat dissipation solution and is widely used in outdoor streetlights, high-power floodlights, and increasingly popular automotive lighting systems. In the field of power electronics, such as various power modules, complex inverters, and efficient rectifiers, the requirements for heat dissipation performance have reached the extreme. MCPCB provides a stable working foundation for these high-power devices. Automotive electronics is another important application direction of MCPCB. From electric vehicle charging piles, on-board inverters to advanced LED lights, MCPCB plays a key role in ensuring the stable operation of vehicle electronic systems under various extreme conditions. In addition, in medical equipment with extremely high requirements for reliability and stability, and in high-frequency equipment that requires stable high-frequency signal transmission, MCPCB is also favored for its excellent performance.
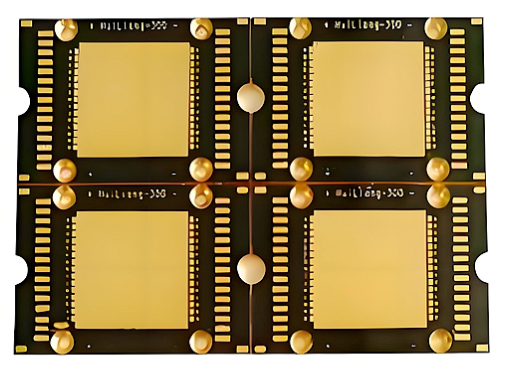
MCPCB Requirements to Meet Demands
Choosing the best MCPCB for your specific application is not a simple matter. It requires comprehensive consideration of multiple key factors to ensure the best balance between performance and cost. First, determine the type of metal substrate. Aluminum substrates are the most used due to their good thermal conductivity and relatively low cost, and are suitable for most application scenarios; copper substrates have better thermal conductivity, but are also more expensive, and are usually used in special occasions with extreme requirements for heat dissipation or need to withstand higher currents. Secondly, the performance of the insulation layer is the key to determining the overall heat dissipation efficiency and electrical safety of the MCPCB. You need to pay attention to key indicators such as its thermal conductivity, compressive strength, and thermal resistance, which will directly affect the heat transfer efficiency of the component and the stability of the system. Of course, the most fundamental consideration is your actual heat dissipation needs. Based on the heat generation and allowable temperature rise of the components in the application, you need to choose an MCPCB with sufficient heat dissipation capacity to control the temperature within a safe range. Finally, cost considerations are an important link that cannot be bypassed in any project. Under the premise of meeting performance requirements, you should strive to find the most cost-effective MCPCB solution among multiple options.
Metal-based circuit boards have successfully broken through the bottleneck of traditional PCBs in thermal management with their excellent heat dissipation capabilities, opening a new era for the design of high-power, high-integration electronic products. As electronic products continue to evolve towards miniaturization, high efficiency and high reliability, the application prospects of MCPCB will become broader and its importance will become increasingly prominent. If you are actively seeking solutions to improve product heat dissipation performance, extend equipment life and enhance overall reliability, then MCPCB is undoubtedly an ideal technology that you deserve to understand in depth and give priority to.
One-Stop HDI PCB Manufacturer and Its PCB Via Filing Capabilities
If you're looking for turnkey HDI electronics manufacturing services (EMS) from hardware development to PCBA fabrication and box-build assembly, you can work with the one-stop HDI PCBA manufacturer PCBONLINE.
Founded in 1999, PCBONLINE has R&D capabilities for HDI projects and EMS manufacturing capabilities, including via filling for stacked vias. It provides 4-to-64-layer HDI PCB fabrication, assembly, and PCBA box-build assembly. You can order various HDI PCBs from PCBONLINE, such as FR4, polyimide (flexible PCB), polyimide + FR4 (rigid-flex PCB), and PTFE/Rogers (high-frequency PCB).
3000m² of production capacity per day for HDI PCBs with builds of 1+N+1, 2+N+2, 3+N+3,4+N+4, and arbitrary interconnection in any layers.
PCBONLINE has hardware and software R&D capabilities for IoT applications requiring HDI design, including PCBA and enclosures.
We can manufacture complex PCBs with stacker vias, via-in-pad, microvias, inlay boards, heavy copper designs, and hybrid and fine structure lay-ups.
Besides HDI PCB fabrication, we have powerful capabilities in fine-pitch assembly for HDI PCB assembly.
We have rich R&D and manufacturing experience for HDI applications such as FPGA boards.
High-quality HDI PCB and PCBA manufacturing certified with ISO 9001:2015, IATF 16949, RoHS, REACH, UL, and IPC-A-610 Class 2/3.
Here'e the PCB via filing capabilities at PCBONLINEL:
- Micriavia filling with copper: laser via size 0.1-0.125mm, priority 0.1mm
- Finished hole size for via-in-pad filling with resin: 0.1-0.9mm (drill size 0.15-1.0mm), 0.3-0.55mm normal (drill size 0.4-0.65mm)
- Max aspect ratio for via-in-pad filling with resin PCB - 12: 1
- Min resin plugged PCB thickness: 0.2mm
- Max via-filling ith resin PCB thickness: 3.2mm
- Making different hole sizes with via filling in one board: Yes
- Via filling with copper/silver: Yes
If you need HDI PCBAs or any other PCBAs requiring via filling, please send your email to PCBONLINE at info@pcbonline.com. We will provide one-on-one engineering support to you.
Conclusion
Via filling is used for creating stacked vias in HDI PCB fabrication, BGA/CSP/QFN IC packaging, and filling PCB via-in-pad with resin during multilayer PCB fabrication. If you need one-stop electronics manufacturing for your HDI PCBA project, contact the one-stop advanced PCB manufacturer PCBONLINE for high-quality PCBA and box-build solutions tailored to your project's needs.
PCB fabrication at PCBONLINE.pdf