PCBONLINE provides PCB box-build assembly services from prototypes to mass production. Below is a video of our turnkey PCB assembly factory and production lines for PCB box build assembly.
PCBONLINE's turnkey PCB box build assembly services cover everything from prototype assembly to mass production and final product packaging. Our factory is equipped with fully automated SMT lines, half-automated DIP lines, advanced inspection systems, and skilled technicians. Our engineering and technical team ensures the highest quality standards for PCBA and box build assembly.
In this article, you'll receive a comprehensive overview of our assembly lines, processes, equipment, and quality control measures — all designed to deliver reliable, production-ready PCBAs and box-build products.
SMT Assembly: High-Speed, High-Precision, and Fully Inspected
At PCBONLINE, surface-mount technology (SMT) assembly is at the heart of our turnkey PCB box build assembly service. Each of our four SMT lines is fully automated, supports the mounting of up to 376 components onto a side of the PCB, and is equipped with 3D SPI and dual AOI systems.
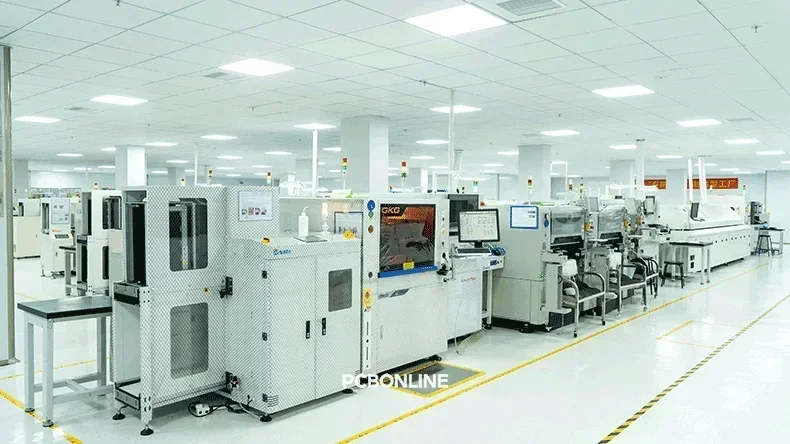
Let's walk through the complete SMT assembly process:
Step 1: PCB Loading and Solder Paste Printing
The process begins by loading bare PCBs onto the automatic loader. Solder paste is then applied using SMT stencils, where it passes through the stencil apertures and deposits onto the PCB pads.
Step 2: Solder Paste Inspection (SPI)
Next, each board passes through a solder paste inspection (SPI) machine, which checks the position, volume, and thickness of the printed solder paste. This step helps detect printing defects early and prevents downstream issues.
Step 3: High-Speed Pick-and-Place with YAMAHA YSM20R
The boards now move to two YAMAHA YSM20R high-speed PNP machines, capable of mounting small SMD components (e.g., 0204, 0306-sized resistors and capacitors).
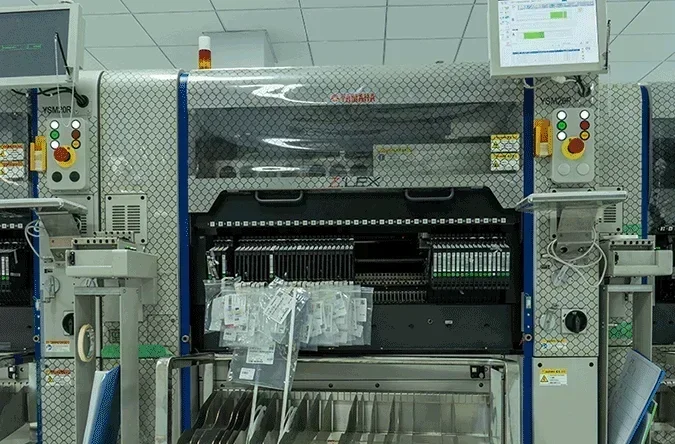
Each YSM20R machine supports 70 SMD slots per side, giving two machines the ability to handle 280 components per board.
Components are rapidly picked from feeders and placed with precise alignment onto the solder-pasted pads.
Step 4: Functional pick-and-place for large components
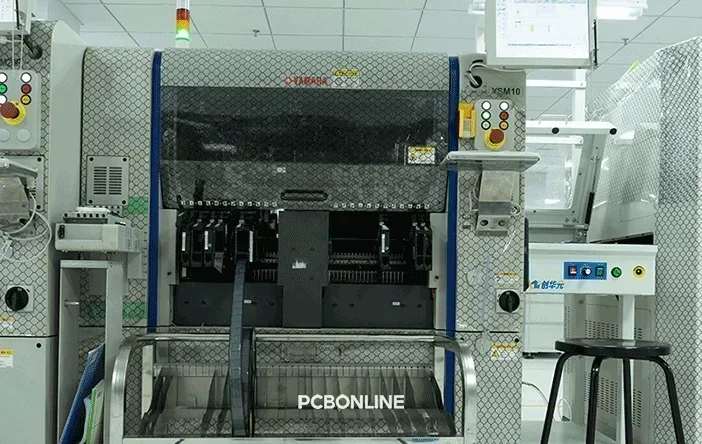
After the small SMDs are mounted, the PCB enters a functional pick-and-place machine — a YAMAHA YSM10 — designed to mount larger or more complex components, including:
- Microcontrollers (MCUs)
- Ball grid arrays (BGAs)
- Connectors
- Sockets
- Switches and buttons
This stage completes the full component placement for the board, with the functional PNP machine supporting 96 large components.
Step 5: Pre-Reflow AOI
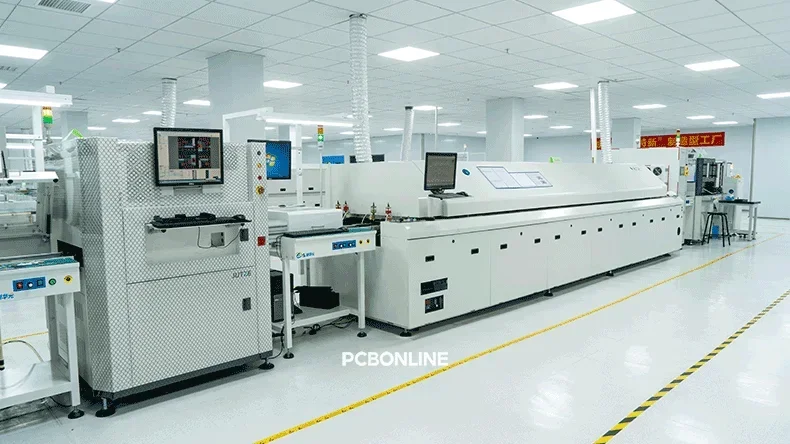
Before soldering, the assembled PCB undergoes pre-reflow AOI (automated optical inspection) to catch issues such as:
- Misaligned or missing components
- Polarity errors
- Wrong components
- Components prone to tombstoning
Identifying problems at this stage prevents waste and rework post-soldering.
Step 6: Reflow Soldering — Forming Reliable Joints
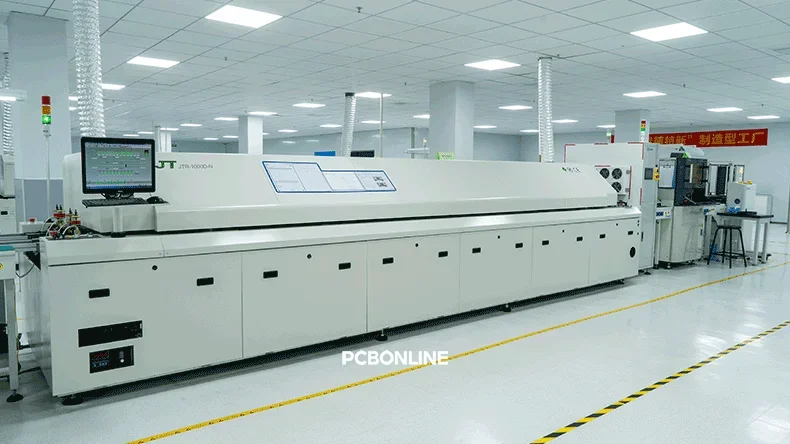
Next, the board enters the reflow oven, where controlled heating causes the solder paste to melt and reflow, creating strong metallurgical bonds between components and PCB pads.
The process follows a precise temperature profile — preheat, soak, reflow, and cooling — to ensure full solder reflow, minimal thermal stress, and prevention of cold joints or solder balling.
During reflow, the melting solder, SMD, and the copper pad undergo a phase change and form a reliable soldering joint.
Step 7: Post-Reflow AOI
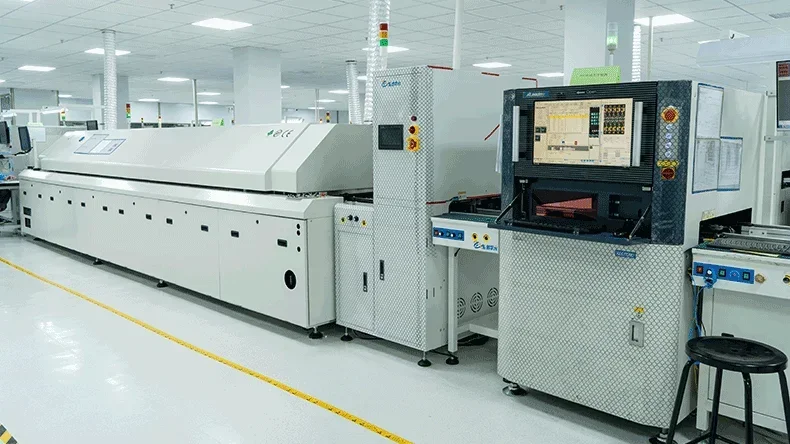
After soldering, the board passes through post-reflow AOI to verify the quality of each solder joint. The 3D AOI inspects:
- Solder bridges
- Cold soldering
- Insufficient or excessive solder
- Tombstoning or component shifts during reflow
Step 8: X-Ray Inspection (for ICs)
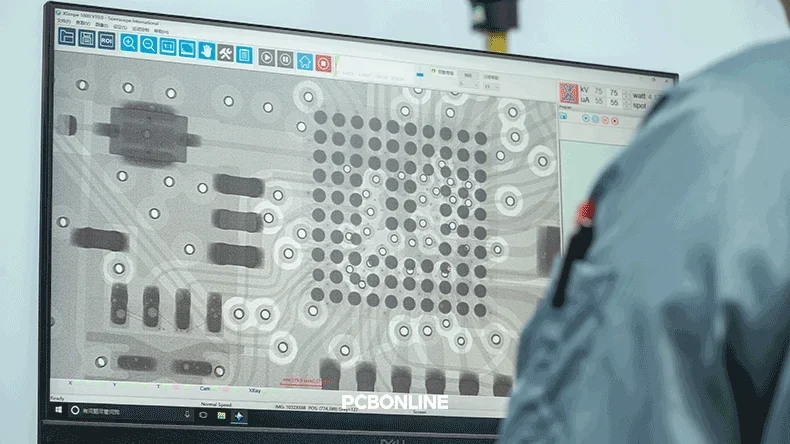
If the board includes BGAs, QFNs, or other hidden-joint components, we perform X-ray inspection after SMT to ensure proper soldering. This is especially critical for microcontrollers and high-pin-count ICs.
First-Article Inspection Before Mass Production
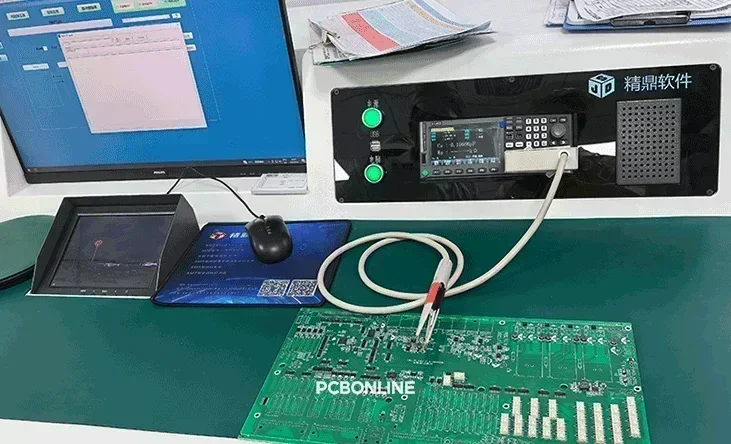
After the prototype SMT assembly is complete, PCBONLINE performs a thorough first-article inspection (FAI). With the FAI, PCBONLINE ensures the prototype is functionally and mechanically sound before moving forward with mass production.
At PCBONLINE, the technician uses the clip probe of the FAI machine to clip to contact every SMD to check if their values are within the tolerance difference range.
By verifying performance at the FAI, we reduce the risk of costly errors later.
Through-Hole (THT) Assembly and Wave Soldering
If your board requires THT or DIP components, our factory is equipped with semi-automated DIP assembly lines to handle large-scale production efficiently.
Technicians insert THT leads into PCB holes manually.
Components prone to float are held down by a custom wave soldering fixture designed by PCBONLINE.
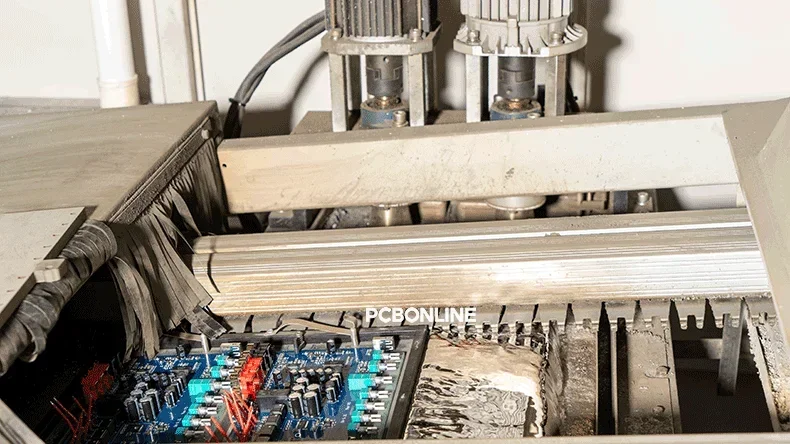
The boards go through flux application, preheating, and wave soldering, where molten solder forms robust joints between the board and component leads.
After soldering, the leads are trimmed to 1-2mm on the PCB underside.
PCBONLINE has handled many power modules and industrial control boards that require high-reliability THT assembly. Our wave soldering process ensures long-term performance even in demanding applications.
Skilled Technicians and Quality-Focused Post-Assembly
At PCBONLINE, our DIP line technicians each have an average of 5 years of experience. Every operator is responsible for their segment of the line, and automated guided vehicles (AGVs) transport fixtures between workstations. All technicians wear anti-static wristbands to prevent electrostatic discharge damage.
After THT and SMT processes are complete, we proceed with post-assembly operations:
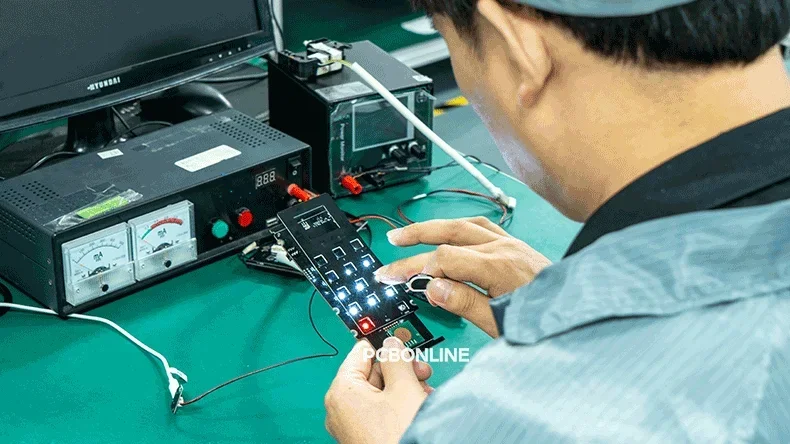
- Touch-up soldering to manually correct any solder issues
- Debugging of the PCBA to ensure functional performance
- Visual inspection for cosmetic and alignment checks
If your PCB box-build assembly project requires transferring the program into the bare IC, PCBONLINE also provides IC programming.
Besides, there are the burn-in test, conformal coating, and PCBA functional test available at PCBONLINE.
Final Integration: From PCBA to Complete Box Build Devices
With PCBA inspection and testing complete, our technicians install enclosures to turn your circuit boards into finished box build devices. These products undergo final inspections and are carefully packaged, ready to ship directly to your end users or distribution centers.
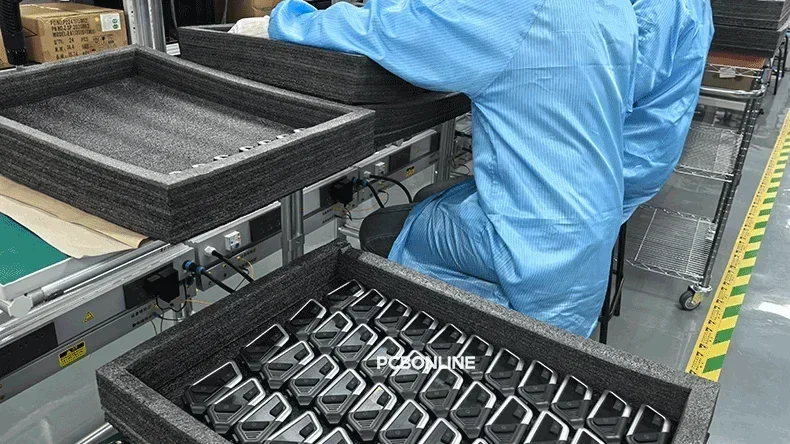
PCBONLINE's PCB box build assembly services cover every step from internal component installation to enclosure integration and application simulation testing, ensuring mechanical, electrical, and aesthetic requirements are fully met.
Professional Component and Material Management
PCBONLINE pays close attention to component integrity and storage, especially for active and high-value ICs. Besides, we manage the SMT stencils, solder paste, and fixtures carefully.
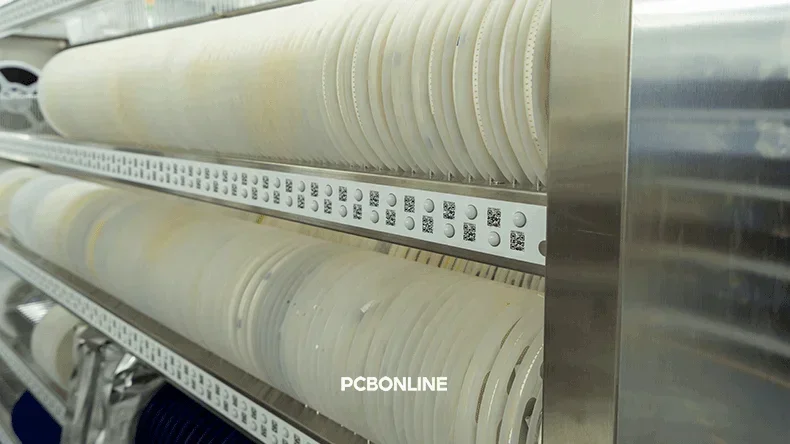
- We conduct X-ray inspections of components before use.
- All high-value parts are stored in a temperature- and humidity-controlled cabinet to prevent degradation or moisture absorption.
- Our SMT stencils are stored and maintained for reorder projects, ensuring consistency across production runs.
- We store and manage solder paste in a smart solder paste cabinet to prevent variation in solder joints.
- All the PCB manufacturing, assembly, and test fixtures are stored and managed on our fixture warehouse shelves.
Rigorous management of the electronic components, SMT stencils, and fixtures is part of the reason for the priority quality of PCBONLINE's PCB box build assembly services. All these details ensure the long-term reliability of the final products.
Why Choose PCBONLINE for PCB Box Build Assembly Services?
Looking for professional PCB box-build assembly services? Founded in 1999, PCBONLINE is a trusted one-stop box build assembly service provider for PCB manufacturing, PCB assembly, value-added, and enclosure installation.
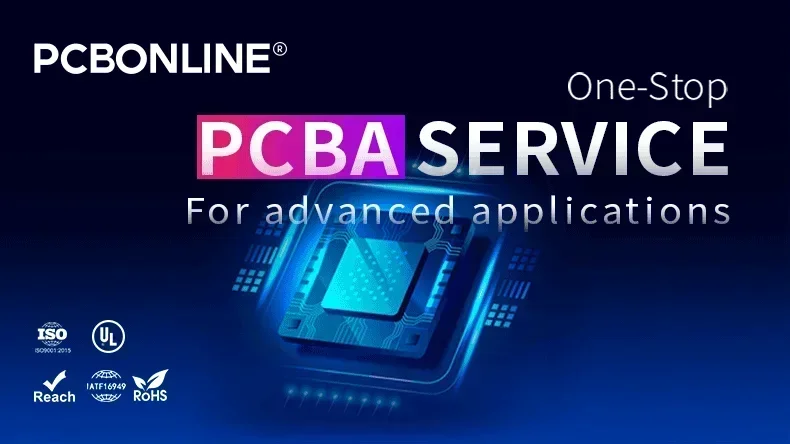
PCBONLINE has two large advanced PCB manufacturing bases, one turnkey PCB box build assembly factory, stable material supply chains, and a dedicated R&D and engineering team. We also maintain long-term partnerships with top fixture and enclosure manufacturers in China.
Provides one-on-one free and professional DFM for PCB, PCBA, and box builds before and during prototyping/sampling, to ensure the manufacturability and project success.
The professionals at PCBONLINE design the PCBA fixtures and manufacturing molds that accurately fit the PCBA manufacturing and test processes.
Complete equipment and capabilities for PCB box-build assembly services, including PCB manufacturing, PCB assembly, and post-assembly, such as functional test, IC programming, burn-in test, and application test.
PCBONLINE manufactures, assembles, and tests from PCBs and PCBAs to box builds as a source factory manufacturer under one roof, from prototypes to bulky production, saving costs and time for you.
High-quality PCBA manufacturing certified with ISO 9001:2015, ISO 14001:2015, IATF 16949:2016, RoHS, REACH, UL, and IPC-A-610 Class 2/3.
PCBONLINE can design the test points for your PCB and offer improvement suggestions for your design if there needs any optimization.
PCBONLINE provides comprehensive PCBA value-added services such as PCBA functional testing, conformal coating, IC programming, burn-in, enclosures, box-build assembly, application test, labelling, packaging, and shipping.
Whether you need prototype assembly, low-volume runs, or high-volume box build production, we have the equipment, experience, and capabilities to deliver superior results. To get a quote for PCB box-build assembly services, email us at info@pcbonline.com.
Conclusion
This article walks you through how PCBONLINE can bring your electronic products to life — from PCB prototype to box build shipping, all under one roof. To ensure the success of your PCB box-build assembly projects, partner with the turnkey PCBA manufacturer PCBONLINE.
PCB assembly at PCBONLINE.pdf