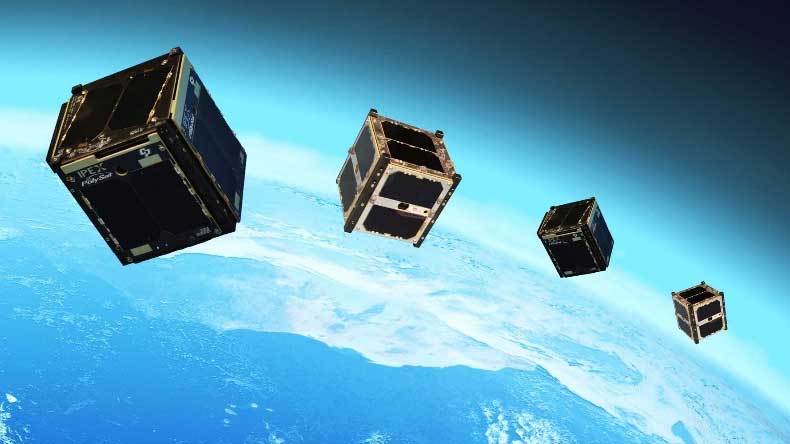
CubeSatellites, or CubeSats, are a small satellite technology offering cost-effective platforms for missions once limited to major space agencies. CubeSats have revolutionized the approach to space exploration, communication, and observation. At the heart of these cube-shaped spacecraft lie Printed Circuit assemblies (PCBA), enabling groundbreaking missions.
In this article, we'll delve into the fascinating world of CubeSats, their challenges, PCB assembly requirements, and the innovative solutions driving CubeSat missions forward!
In this article:
Part 1: What is a CubeSat Part 2: Subsystems or PCBA Modules of CubeSats Part 3: ArduSat and other examples of CubeSat Part 4: CubeSat Challenges and PCBA Requirements Part 5: One-Stop CubeSat and Aerospace PCB Assembly ManufacturerWhat is a CubeSat
A CubeSat is a small satellite with a standardized form factor of 10cm cubes and a maximum mass of 2kg. They are launched either from the International Space Station or as secondary payloads on launch vehicles.
The Development of CubeSate technology
The first CubeSat was developed in 1999 to foster skills in satellite design, manufacturing, and testing for scientific research and technology exploration.
With the progression of time, the CubeSats have started to serve various other functions, including conducting miniaturized experiments, Earth observation, and amateur radio communication. They are used to demonstrate spacecraft technologies for small satellites and to test concepts that may not justify the cost of larger satellites.
CubeSats are also employed for scientific experiments with unproven theories, as their low cost can substantiate higher risks. The Nanosatellite and CubeSat Database lists over 4,000 CubeSats launched or planned since 1998, highlighting their widespread adoption and usage.
Design standards of CubeSatellite
The rise of micro and nano-satellites led to the initial design standards concerning weight and size. Among these standards, the CubeSat 1U standard is widely recognized and utilized. It establishes the physical dimensions, weight, and volume specifications for nanosatellites.
A single unit (1U) of a CubeSat must adhere to a cubic shape measuring 10cm on each side, corresponding to a volume of 1 dm³, and its mass must not exceed 1.33kg. A CubeSat 1U is shown as the first image (left to right) in the next figure.
By combining multiple single units, it's possible to increase the size, internal space for systems, and maximum weight. Different size standards of CubeSats are depicted in the above Figure. Each unit can accommodate various subsystems, referred to as payloads, whose specifications are tailored to the mission for which the CubeSat is designed.
Subsystems or PCBA Modules of CubeSats
CubeSats consist of multiple subsystems, each presenting unique complexities, costs, and testing requirements. There are several subsystems of a CubeSat; commonly found subsystems in nano-satellites include solar panels, antennas, an on-board computer (OBC), an attitude determination and control system (ADCS), a power management unit, a radio module, and one or more secondary payloads. The following image represents a stacked PCBA structure of a CubeSat encompassing different subsystems.
Following are some necessary subsystems or PCBA modules of a CubeSat:
Communication module
The Communication subsystem serves the exchange of data between the satellite and ground stations. It includes antennas, transceivers, and sometimes amplifiers, data rate, and communication protocol. The PCBA manufacturing cost of the communication module can vary a lot depending on quality factors and the specific components used.
Power module
The Power Subsystem is CubeSat's essential energy hub. It generates and supplies power to all other subsystems. It encompasses solar panels, batteries, and power management circuits. The power module's complexity depends on CubeSat's power requirements and the efficacy of the solar panels and batteries. The power management circuit ensures efficient power distribution among subsystems and oversees battery charging and discharging. Due to the necessity for reliable and efficient components, the PCBA costs for this subsystem are relatively high.
On-board Computer
The On-Board Computer (OBC) is the central processing unit of the CubeSat, coordinating its operations. It undertakes tasks such as data processing from other subsystems, command execution, and overall CubeSat management. The complexity of the OBC depends on what it needs to do. The OBC must effectively manage the data processing demands of the mission and withstand the rigors of space. The PCBA costs of the OBC can fluctuate a lot based on its complexity.
Attitude determination and control (ADCS)
The Attitude Determination and Control System (ADCS) is responsible for determining and managing the CubeSat's orientation. The ADCS's complexity aligns with the mission's precision demands. Missions necessitating exact pointing entail a more intricate ADCS setup. Sensors must exhibit adequate precision to discern the CubeSat's orientation, while actuators must have the capability to adjust it.
Payload
The Payload constitutes mission-specific equipment housed within the CubeSat. It comprises cameras, sensors, or other scientific instruments. The unique demand of the mission determines the complexity of the payload module. For instance, CubeSats tailored for Earth observation might feature high-resolution cameras, whereas those designated for scientific research might carry spectrometers or similar instruments. Payload PCBA design must align with mission requirements and withstand space challenges.
ArduSat and other examples of CubeSat
ArduSat is a nanosatellite built on the Arduino platform based on the CubeSat standard. It is equipped with a set of Arduino boards and sensors. It offers the opportunity for the public to leverage these components for innovative endeavors during their space missions.
The above image is an illustration of ArduSat. It consists of a payload containing a camera and different environmental sensors for space observations, an Ultra High Frequency (UHF) communication module, a power module along with solar sensors, and a flight control system.
All these modules have been discussed in the above sections explaining the functionality and need of each subsystem. With these individual module PCBs, there is a mechanical structure of ArduSat equipped with antennas and an antenna deployment system. Along with ArduSats, there are other examples of CubeSats like CUTE-I, DTUsat, QuakeSat, TUSat1, etc.
CubeSat Challenges and PCBA Requirements
Flight attitude issues are a big challenge in CubeSat operations despite advancements in design and manufacturing. These issues come from various factors, such as non-uniform solar radiation, torque from solar panels, and the Earth's magnetic field. Aerospace systems, whether on aircraft, spacecraft, or satellites, face tough environmental conditions like vibration, temperature fluctuations, and pressure changes.
Furthermore, the CubeSat systems often have to operate for a long time, whether it's for earth observation or scientific experimentation.
Besides, the CubeSat's subsystems have a lot of interconnected electronic components. If a single PCB or one part fails, it can mess up the whole system.
For instance, an ADCS system of CubeSat is crucial for navigation, but also holds its challenges. Among ADCS technologies, Magnetorquer or Magnetic Torquer is a cost-effective solution for CubeSat attitude adjustment. The Magnetorquer PCB for CubeSats deals with flight attitude challenges by integrating coils for torque, sensors for flight data monitoring, communication interfaces for ground station interaction, and control algorithms for adjustment decisions. Gyroscopes, magnetometers, and accelerometers capture flight attitude data, which a microcontroller or FPGA processes to generate control signals. These signals control the current and voltage within the torquers, generating torque to adjust the CubeSat's attitude. Therefore, each PCB needs to work perfectly for the CubeSat's seamless operation.
To ensure reliability in challenging environments, you need to keep certain factors in mind in the CubeSat box build assembly design. The following are some of the important factors in designing a CubeSat PCB.
Quality materialsTo design CubeSat PCBs, durable and reliable materials available on the market are necessary because the cost of maintenance is high and, in many cases, impractical.
Heavy copper technologyIt is recommended that heavy copper layers (2 to 6 oz/ft2 or more) are used to facilitate natural heat dissipation without additional cooling systems.
Reference standardsIn aerospace PCBs, it is crucial to follow specific reference standards such as IPC 6012DS and AS/EN 9100 to ensure minimal maintenance, rigorous safety, and high-quality standards.
Routing guidelinesIt is recommended to utilize the appropriate sizing of PCB traces to handle maximum current load.
ComponentsUse mil-spec grade components with tight tolerances, and remember to identify high-frequency and low-frequency components.
Cost savingThe cost of CubeSat PCB assembly varies based on assembly type and complexity, with precision and accuracy being key factors. The PCBA manufacturer PCBONLINE can save costs by purchasing components in bulk from reputed suppliers and alternative components with the same functions and certifications, different assembly methods and designs meet industry standards.
Quality assurance processesCubeSat PCB assembly demands higher precision than industrial PCBs due to the need for flawless operation in harsh environments. Therefore, CubeSat PCBs undergo specialized processes to cope with the routine working conditions in space. The PCB assembly process at the one-stop PCBA manufacturer PCBONLINE involves:
- Cleaning PCBs with de-ionized water and compressed air to prevent defects
- Automatically applying solder paste with stencils, and using automated pick-and-place machines and lead-free reflow ovens for assembly. During the SMT (surface-mount) assembly, there are 3D precise inspections, including solder paste inspection (SPI), X-ray inspection, and automated optical inspection (AOI).
- In PTH (through-hole) assembly, selective soldering targets of specific areas for soldering are soldered to minimize heat exposure to sensitive components.
- Rigorous testing is conducted on aerospace PCBAs, including functional testing, thermal aging, temperature variation testing, vibration testing, and pressure change testing.
- Protective coating of the components on the printed circuit board assembly. A conformal coating is applied to protect against harsh environmental conditions such as moisture, chemicals, and temperature variations.
- Final product box build assembly. The PCBAs for different subsystems are assembled and installed with the enclosure to be a CubeSat.
- Application simulation testing is applied on the CubeSat box build assembly to simulate and evaluate performance.
One-Stop CubeSat and Aerospace PCB Assembly Manufacturer PCBONLINE
If you need high-quality and affordable PCB assembly for CubeSat and other aerospace applications, you can cooperate with the advanced PCBA manufacturer PCBONLINE. Founded in 1999, PCBONLINE has two large advanced PCB manufacturing bases, one EMS PCB assembly factory, and an R&D team. It offers one-stop PCB assembly until you get the modules and final product box builds.
You can have PCBA manufacturing at one stop, including PCB fabrication, component sourcing, PCB assembly, conformal coating, and box-build assembly.
PCBONLINE is an advanced electronics manufacturer with rich experience in PCBAs for aerospace, defense, medical, automotive, computer, and communication applications.
The professional engineers at PCBONLINE can greatly reduce your CubeSat PCBA costs by selecting more affordable alternative components without functional and quality sacrifice.
PCBONLINE's aerospace PCB assembly follows IPC-A-610 Class 3 and is certified with ISO 9001:2015, IATF 16949, RoHS, REACH, UL, IPC 6012DS, and AS/EN 9100.
The engineers at PCBONLINE have more than 20 years of experience and will provide one-on-one engineering support throughout the project.
Whether you are from an original equipment manufacturer, research institute, or business maker, you will find it hassle-free to work with PCBONLINE for CubeSat and aerospace PCB assembly. If you want to get a quote or technical assistance, you can send your inquiry to PCBONLINE by email at info@pcbonline.com.
Conclusion
The CubeSats represent a remarkable advancement in space exploration, offering a wide range of scientific, commercial, and educational missions. Their compact size and standardized design have allowed small organizations, universities, and even individuals to participate in space activities. Whether you are a seasoned professional or a budding enthusiast, PCBONLINE offers tailored R&D and PCBA manufacturing services to bring your CubeSat to life!
PCB assembly at PCBONLINE.pdf