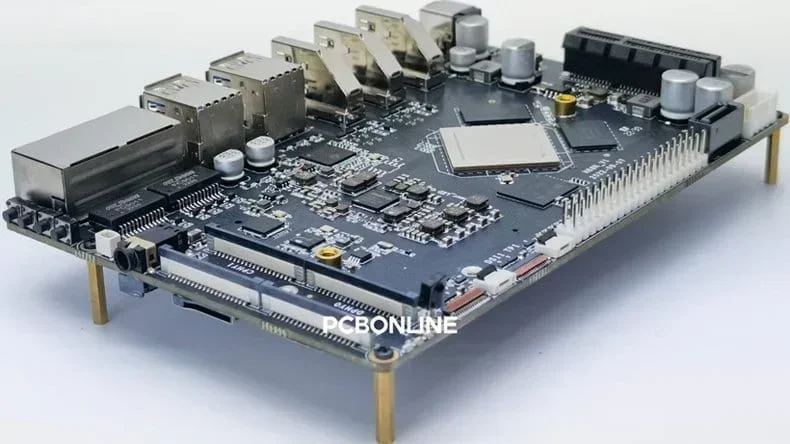
In electronics manufacturing, the industrial grade means high reliability and high quality. Suppose your project aims for middle or high-end applications, even though it is a consumer electronics device. In that case, you can require its PCB (printed circuit board) manufacturing to be industrial-grade from the PCB manufacturer.
In this article, you can learn about the industrial PCB manufacturing standards, the key points that determine whether the industrial PCB project succeeds or not, and 4 industrial-grade PCB project examples manufactured by the industrial PCB manufacturer PCBONLNE.
In this article:
Part 1. Industrial PCB and Its Manufacturing Standards Part 2. Industrial PCB Materials and Manufacturing Part 3. Key Points in Industrial PCB Projects: BGA soldering Part 4. Industrial PCB Project 4 Examples Part 5. One-Stop Industrial PCB manufacturerIndustrial PCB and Its Manufacturing Standards
Printed circuit boards are custom-designed and used for carrying components providing electrical connections and mechanical support. For industrial and other high-current applications, the PCB also assists the thermal dissipation of the system through the PCB substrate.
The features of industrial PCBs include:
- Industrial PCBs have higher reliability and performance than commercial-grade PCBs.
- Their service life lasts 10 years with very low error rates (<1%).
- Industrial PCB usually requires high current capacity, high thermal dissipation, or the ability for long-period working.
On an industrial PCB PCB, the components should be industrial-grade ones. That means, the components on the industrial PCB should meet the below specification standards:
- Working temperatures: -40°C ~ 85°C (can extend to 105°C)
- Industrial chip quality standard: ISO 9000
- Industrial-grade IC standard: JESD47
- Industrial-grade IC chips' error rate < 1% (100ppm)
- Industrial electronics service life: 10 years (according to 15% working time each day)
Now, you've learned the components requirements mounted on the industrial PCBs. Let's go back to the industrial PCB board itself.
Are there any standards for industrial PCBs?
Yes.
An industrial PCB manufacturer should meet the following quality standards:
- ISO 9001 - the international quality management system standard
- ISO 14001 - requires that industrial PCB manufacturing is environmentally friendly
- IPC-A-600 Class 2/3 - The second and highest PCB acceptance standards. Industrial PCB manufacturing is of high reliability and strict tolerance requirements.
Besides, industrial PCB assembly should also provide high-reliability soldering strength. Industrial PCB assembly should meet the IPC-A-610 Class acceptance standards, which means the PCB assembly process must follow all the IPC criteria.
Industrial PCB Materials and Manufacturing
Except for the different standards and details, industrial PCBs have no differences from PCBs used for the other fields, including the PCB materials and manufacturing steps.
Industrial PCB materials
Industrial PCBs usually need to dissipate heat quickly so the PCB materials can be:
High-Tg FR4: FR4 materials are glass fiber of the flame retardant level 4. It is a cost-effective and common PCB material. FR4 materials of high Tg means the FR4 PCB can withstand the highest working temperature of 135°C and above.
Metal core (aluminum and copper): Metal-core PCBs use aluminum or copper as the substrate that can dissipate heat quickly. The aluminum PCBs are usually single-layered or double-layered. Copper-based PCBs can be 1 to 8-layered. This is because it can use the copper bumps to directly transfer heat from the components while separating the electrical network.
Ceramic (aluminum nitride and aluminum oxide): Aluminum nitride PCBs and aluminum oxide PCBs are both ceramic PCBs. Ceramics are insulation materials with excellent thermal dissipation and resistance. They can be used for industrial applications such as COB LEDs, IGBTs, patching beverage can lids, etc.
Industrial PCB manufacturing
Industrial PCB manufacturing usually includes the following steps:
Cut laminate: Cutting and filleting the laminates to be the PNL (panelization) board's size.
Generating inner layer circuits: Patching a circuit-graphic film above the laminate, going through exposure and development to create the inner layer circuits, and etching to form the circuit lines and PCB pads. Having an AOI (automated optical inspection) for each circuit layer.
Lamination: Going through the browning reaction, riveting, stacking layers, laminating the inner layers, drilling the fiducial points, and profiling the PNL board. It makes the PCB core.
Drilling PTH holes and plating: Using drills to mechanically drill the through holes, going through the electroless plating copper process, and plating a copper layer on the hole walls.
Generating outer layer circuits: Patching a dry film above the PCB core, going through the exposure and development process, secondary copper plating, tin plating, removing the dry film, and etching away the non-circuit-area copper to create the outer layer circuits.
Applying solder mask and silk screen: Using the silkscreen method to print the PCB inks on the PCB and bake them.
Applying surface finish: Using various methods to apply the required surface finish on the PCB pads to protect the copper pads for SMT assembly.
Profiling: Routing the PNL board to the required dimension and size.
Testing and final quality control: Having the electrical connection test, flying probe test, and final quality assurance inspections.
After the PCB manufacturing, the PCB boards and components are soldered through the SMT and PTH assembly to make the industrial semi-products. After box-build assembly, they are installed with enclosures and become the final products or systems.
Key Points in Industrial PCB Projects: BGA soldering
The devil is in the details.
For industrial PCB projects, one key point is BGA soldering.
The bubble rate of soldering the BGA must be below 10% and should be as small as possible.
The industrial PCB manufacturer PCBONLINE can control the bubble rate of 3% in soldering the BGA.
Let's explore BGA soldering below.
BGA and its soldering bubble rate
A BGA is a common FPGA chip package type. Its solder balls are in a high-density grid shape and are connected to the bottom of the chip package.
It can provide more functional input and output pins and can be used in high-power industrial applications.
Why are there the bubbles in BGA soldering?
During SMT assembly, after the solder paste hot-melting and solidifies on the BGA pad, a certain proportion of bubbles will occur.
The bubbles will reduce the mechanical strength of the solder joint, can lead to short circuits, and affect electrical connections.
According to IPC standards, any solder ball voids bigger than 25% at the BGA pad inspection area are considered defects.
For industrial PCBs, when the bubble rate is more than 10%, it may affect the reliability and performance of the BGA and the entire PCB board.
At the industrial PCB one-stop manufacturer PCBONLINE, the BGA welding quality control standard is to control the bubble rate below 5%. It ensured welding quality and final product performance.
And we can control it to be 3%.
As shown in the picture above, the industrial PCBA is the RK3588 control board manufactured by PCBONLINE. Its BGA bubble rate is less than 3%<. The breakthrough of this technology tests the production capability, the precision of the equipment, and the engineers' experience.
Industrial PCB Project 4 Examples
Having learned the process and key points for industrial PCB projects, you can view 4 real example projects below!
Project: Cloud Server Assembly
Service: OEM
Support details:
- Manufacturing 12-layer HDI back-drilled PCBs
- Procurement of components and sheet metal enclosure
- One-stop machine assembly and production
- Software burn-in and electrical function testing
- IPC Class 3 / Industrial Grade Quality Standard
Project Features:
Reduced procurement costs for clients by 26% through supply chain optimization, with support for installment payments.
Project: Industrial Control Motherboard
Service: One-stop PCBA
Support details:
- Manufacturing 10-layer HDI PCBs
- Procurement of components
- Completed PCB Assembly
- Software burn-in and electrical function testing
- IPC Class 3 / Automotive Grade Quality Standard
Project Features:
Free DFM includes PCB file impedance control line optimization to reduce signal distortion; grouping and concentrated placement of computational chips and power management chips to improve heat dissipation; and use of shielding measures to reduce EMC interference.
Project: IoT Lighting Control Motherboard
Service: One-stop PCBA
Support details:
- 95% of the components are procured by PCBONLINE;
- Design of functional test fixtures
- Software programming and aging tests
- PCB and assembly are produced in a one-stop process at PCBONLINE’s factory
Project Features:
Recommending communication modules produced in China helps customers reduce costs by 16% while maintaining performance.
Installment payment support is available.
We assist customers in simplifying their supply chain process with scheduled and timely deliveries, alleviating their inventory management costs.
Project: Smart Projector ODM
Service: From R&D to mass production
Support details:
- AD structure design, plastic mold manufacturing (outsourced)
- Motherboard hardware and software design
- Develop user interface software
- From prototype to mass production
- Industrial-grade Quality Acceptance Standards
Project Features:
Intellectual property belongs to the client.
A full refund of the initial R&D costs will be provided once the bulk order reaches the agreed quantity.
Before the design phase, based on the customer's requirements for low cost and compact size, we select the most cost-effective main control chip and consider mold production costs to maximize cost savings for the customer.
One-Stop Industrial PCB Manufacturer
You can work with the advanced PCB source factory manufacturer PCBONLINE for industrial PCBs under one roof. In industrial PCB project manufacturing capabilities, we have:
- Two large advanced PCB manufacturing bases for industrial PCBs,
- One turnkey PCB assembly factory for industrial PCBAs,
- Stable material supply chains and strategic cooperation with the mainstream MCU manufacturers for all electronic components,
- Long-term cooperation with the top 3 mold and enclosure manufacturers in China for jigs/textures, molds, SMT stencils, and plastic/metal enclosures.
- An R&D team and professional CAM engineers for project development and DFM (design for manufacturing).
PCBONLINE offers free DFM before and during industrial PCB prototyping/sampling to ensure the success of batch production, including checks of Gerber and BOM, jig/fixture/PCB stencil design, manufacturing process and testing designs, and solving all issues throughout the project to ensure seamless manufacturing.
PCBONLINE can provide or assist R&D for your industrial PCB project, including hardware and software R&D, schematics, PCB layout, and enclosure design.
Completing industrial PCB projects under one roof, including PCB manufacturing, component sourcing, PCB assembly, PCBA value-added and testing/inspections in the post-assembly stage, and box-build assembly.
High-quality industrial PCB/PCBA manufacturing meeting your application demands, including ISO 9001:2015, ISO 14001:2015, IATF 16949:2016, RoHS, REACH, UL, IPC-A-610 Class 2/3 and IPC-A-610 Class 2/3.
No matter what quantity you want, we always prioritize quality and provide service and support meeting and exceeding your expectations.
Besides industrial PCB projects, if you need higher-performance PCBs - automotive and medical-grade, PCBONLINE can also meet your project requirements! Don't hesitate to contact info@pcbonline.com.
Conclusion
Industrial PCBs have higher reliability and performance than consumer-grade electronics. Not only industrial devices but mid to high-end consumer devices can also use industrial PCBs for their production. If you need industrial PCBs, choose PCBONLINE as your one-stop manufacturer with free DFM and the best reliable quality.
PCB assembly at PCBONLINE.pdf