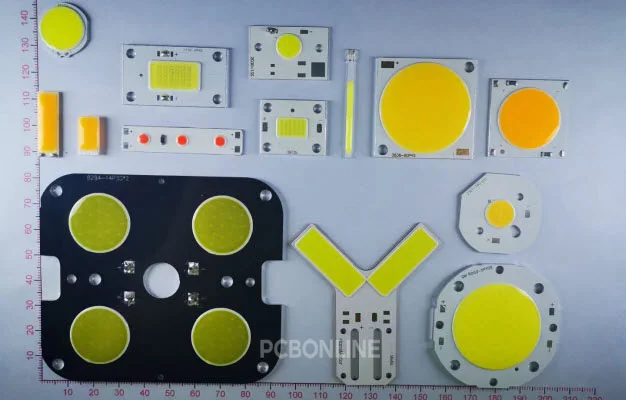
What is a COB LED PCB? COB means chip-on-board, and COB LED PCB (printed circuit board) refers to a PCB directly bonded with COB LEDs rather than surface mounted with SMD (surface-mount device) LEDs.
If you want to develop a COB LED product by designing a COB LED PCB, learn more about what a COB LED PCB is, including the different types of COB LED PCBs and two COB bonding methods on the PCB.
In this article:
Learn about COB LED PCB Types of COB LED PCB and Their Applications COB LED PCB Bonding: Wire Bonding and Flip-chip Bonding COB LED PCB Bonding: Wire Bonding and Flip-chip BondingLearn about COB LED PCB
A COB LED PCB is designed to address the thermal dissipation of the LEDs.
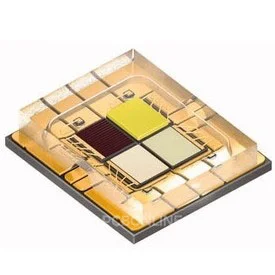
In a COB LED PCB, many LED chips are directly adhered to a thermally conductive PCB board and encapsulated with silicon or epoxy resin.
A uniform phosphor coating is applied to the LED chips to convert blue or purple light into white or other colors like red and green. The resin encapsulating the COB LEDs is transparent.
Unless it is used for plant grow lights or other applications requiring a special light spectrum, additional phosphor powders are added to the resin encapsulating the COB LEDs.
Compared to a traditional SMD LED PCB, a COB LED PCB offers many advantages.
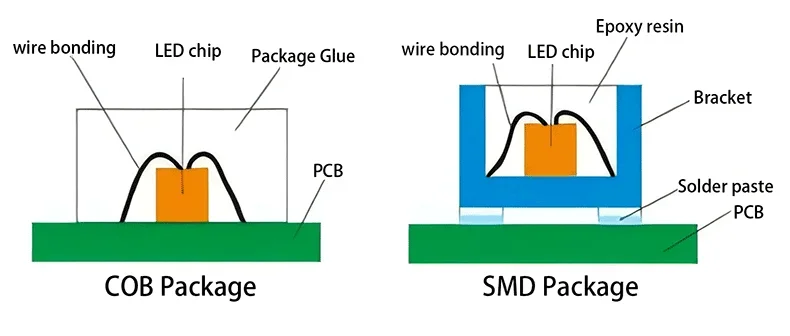
- Lightweight: The thickness of the COB PCB ranges from 0.4mm to 1.2mm. A COB LED PCB reduces about 1/3 of the weight of an SMD LED PCB.
- Wide lighting angle: with a shallow well spherical light emission, COB LED products emit light with an angle greater than 175° close to 180°. This wide lighting angle offers soft light effects and excellent optical diffusion.
- Impact and pressure resistance: The COB LEDs are encapsulated to form a smooth and hard convex spherical surface. It is resistant to impacts and pressure.
- Excellent thermal dissipation: The LED chips are bonded to the PCB so the heat is transferred from the LEDs to the PCB substrate directly. It provides superior heat dissipation, eliminates light decay, and extends the service life of LED products.
- Waterproof: LEDs are the critical components of an LED product. In a COB LED product, the LEDs are encapsulated with silicon or epoxy resin so they are waterproof and dust-proof. If the enclosure of the LED product is sealed carefully and the cable entry point uses a silicon o-ring with thread locking, the LED product can even work in underwater environments.
Besides, a COB LED PCB can work in temperature ranges from -30°C to +80°C.
Types of COB LED PCB and Their Applications
COB LED chips are high-power LEDs so the substrate of the COB LED PCB should be thermally efficient.
Based on the different PCB substrate materials, there are copper core, flexible, and ceramic COB LED PCBs.
Copper-core COB LED PCB
Copper-core PCBs whose thermal pads are directly connected to the copper substrate provide the highest thermal conductivity among all PCBs.
If the heat is conducted through a prepreg layer to the PCB substrate, the copper-core PCB's thermal conductivity is still better than aluminum PCBs.
Copper-core COB LED PCBs are used in high-power LED applications, such as industrial and outdoor lighting.
For example, below is a copper-core COB LED PCB manufactured by PCBONLINE for high-power LED lights.
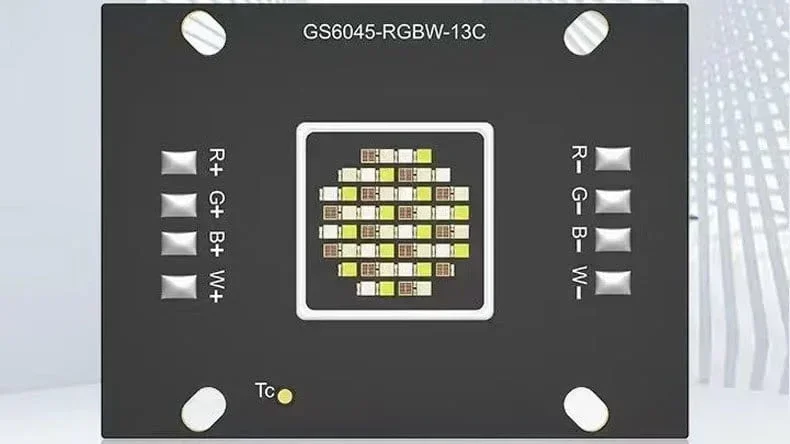
Flexible COB LED PCB
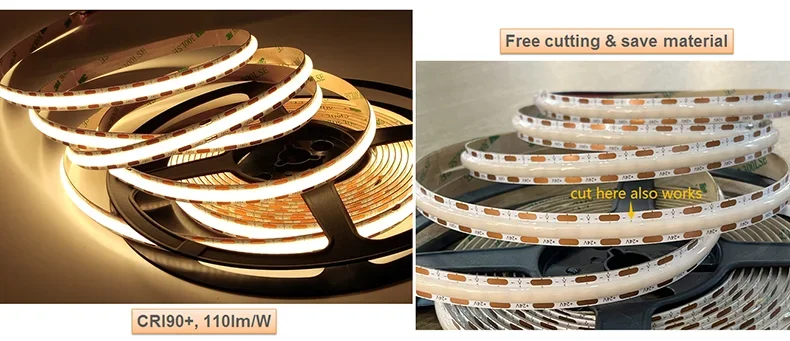
By using the flexible material polyimide as the substrate, insulation, and coverlay materials, a flexible COB LED PCB and light can bend and shape according to design requirements. The structure of flexible COB LED lights is simple and their costs are much lower than traditional LED displays and screens.
Wearable lights like LED strips and LED screens/displays can use flexible COB LED PCBs.
For example, below is a flexible COB LED PCB manufactured and assembled to be the final product by PCBONLINE for miners' headlights.
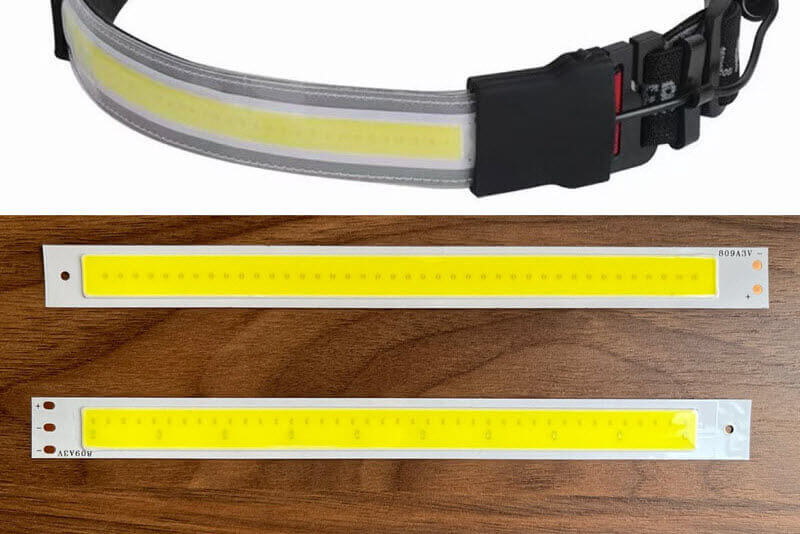
Ceramic COB LED PCB
Ceramic materials for PCBs include aluminum oxide (Al2O3) and aluminum nitride (AlN), providing excellent thermal conductivity and electrical insulation.
Ceramic PCBs offer the second-best thermal conductivity only after thermoelectric separation copper core PCBs and the best temperature resistance.
Besides, ceramic PCBs provide very small dielectric constant (DK) and dielectric loss (Df) and strict impedance control with only 0.05% tolerance.
High-end LED applications can adopt ceramic COB LED PCBs, providing the best lighting effects, long service life, and reliability.
For example, below is a ceramic COB LED PCB designed and manufactured by PCBONLINE used for high-end swimming pool lights.
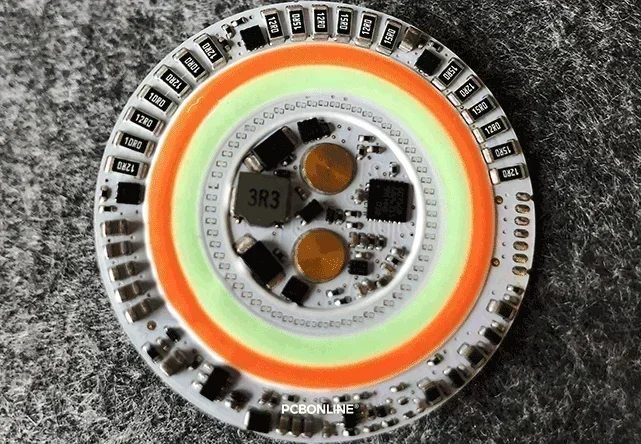
Hybrid COB LED PCB
A hybrid substrate PCB for COB LED lights is usually a ceramic PCB bonded with the light source inlaid in the larger copper-base PCB.
Such a hybrid COB LED PCB provides superior thermal dissipation and is used for high-power LED applications like stage lights and photography lights.
For example, below is a hybrid COB LED PCB manufactured by PCBONLINE for stage lights.
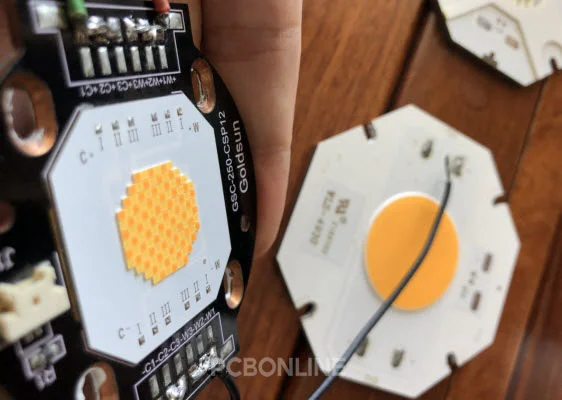
COB LED PCB Bonding: Wire Bonding and Flip-chip Bonding
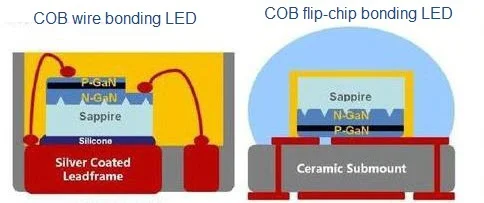
The LED chips are integrated to mount on the PCB, how do they electrically connect with the PCB and emit light? They are wire-bonded or flip-chip-bonded on the PCB to electrically connect.
Wire bonding
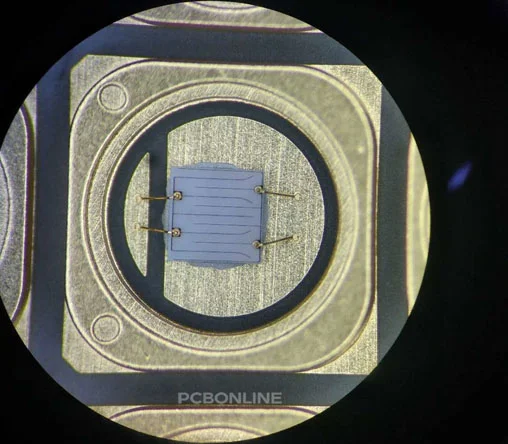
Wire bonding involves connecting LED chips to the PCB using gold or aluminum wires. This traditional method is cost-effective and widely used.
However, the two wires take up some light-emitting area, affecting the light-emitting efficiency.
Besides, the thermal from the P-N joint of the LED has to go through the LED substrate to the PCB, so its thermal conductivity is not that good.
COB LEDs using wire bonding are commonly used in small-power COB LEDs.
Flip-chip bonding

Flip-chip bonding, without any wires, mounts LED chips directly onto the PCB with solder bumps.
The LED chips are inverted, the LED substrate is peeled off, and the chip material is transparent.
The light excited by the light-emitting layer is directly emitted from the other side of the electrode.
This method offers better thermal performance and higher light-emitting efficiency. It is getting popular for COB LED lights, especially the high-power ones (LED chip > 1W).
Turnkey COB LED PCB Manufacturer PCBONLINE from PCBA to Box-builds
PCBONLINE is a one-stop COB LED PCB manufacturer, providing turnkey COB LED PCB manufacturing until you receive the final products.
Founded in 1999, PCBONLINE has two large advanced PCB manufacturing bases for COB LED PCBs, one turnkey PCB assembly factory for COB LED PCB assembly and box-build assembly, stable material supply chains, and strategic cooperation with electronic component manufacturers, and long-term cooperation with the top 3 mold and enclosure manufacturers in China for jigs/fixtures, molds, and enclosures.
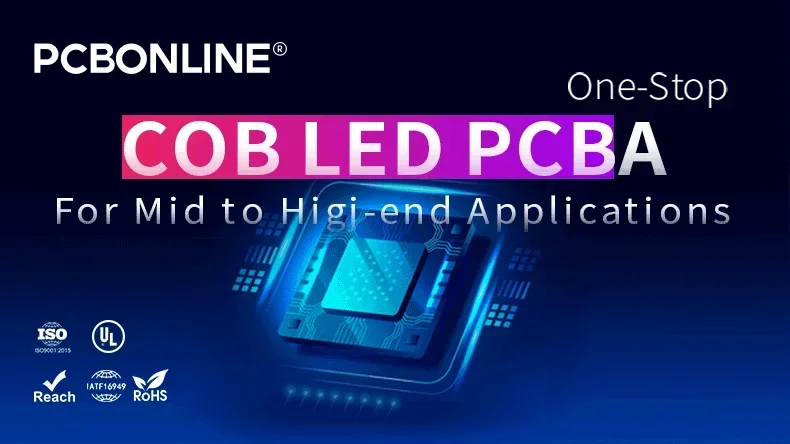
Turnkey COB LED PCB manufacturing, from flexible/ceramic/copper-core PCB fabrication, LED chips sourcing or custom making, COB bonding, and PCB assembly, to the COB LED appearance packaging.
PCBONLINE has mature techniques of COB LED wire bonding and flip-chip bonding.
PCBONLINE can adjust the COB LED light wavelength according to the specified optical parameters and make them RGB or RGBW.
Free and professional design for manufacturing (DFM) and one-on-one engineering support throughout your COB LED PCB projects.
PCB manufacturing is IPC-A-600 compliant, and COB LED assembly is IPC-A-610 Class 3 compliant.
PCBONLINE manufactures, assembles, and tests COB LED PCBs to assemble them with the enclosure to be the final products under one roof, from prototypes to bulky production.
High-quality COB LED PCB fabrication and assembly certified with ISO 9001:2015, ISO 14001:2015, IATF 16949:2016, REACH, RoHS, and UL.
PCBONLINE has worked on many COB LED PCB, PCBA, and box-build assembly projects for different LED applications, such as automotive lights, underwater lights, ship lights, yacht lights, miners' head lights, airport outdoor LED displays, COB LED strips, stage lights, spotlights, and photography lights. If you feel interested in COB LED PCBs, PCBAs, and box-build assembly from PCBONLINE, feel free to send your inquiry by email at info@pcbonline.com.
Conclusion
This blog introduces COB LED PCBs comprehensively. LED chips are integrated and bonded to the PCB board directly, providing excellent lighting effects and thermal conductivity. To bond the LED chips on the PCB, the methods include wire bonding and flip-chip bonding. To have your COB LED project manufactured with reliability and at one stop, work with the turnkey COB LED PCB manufacturer PCBONLINE.
PCB fabrication at PCBONLINE.pdf