A ceramic PCB is a unique process board in which copper foil is directly bonded to alumina ( Al2O3), aluminum nitride ( AlN), beryllium oxide (BeO), or silicon carbide (SiC) ceramic substrate surface (single-sided or double-sided) at high temperatures. A ceramic PCB has more heat transfer properties than metal core PCBs and has good high-frequency performance and electrical properties. It also has a low expansion coefficient (CTE). A ceramic PCB is considered to have the best properties of both FR4 and metal-core PCBs.
This article will give you a clear overview of the ceramic PCBs from the below parts.
Part 1: Ceramic PCB Base Materials
The ceramic compound material used for ceramic PCBs is a mixture of metallic oxides and nitrides. Commonly used materials are:
- Aluminum Nitride (AIN)
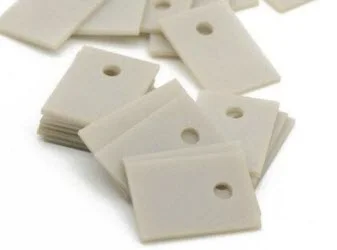
- Aluminum oxide (Alumina) (Al2O3)
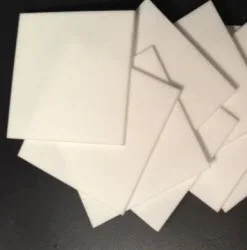
- Beryllium oxide (BeO)
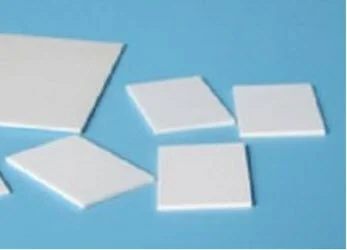
Aluminum oxide ceramic (Al2O3) has a thermal conductivity that ranges from 24W/mK up to 30W/mK, and aluminum nitride ceramic has a thermal conductivity that ranges from 150-320W/mK. Aluminum oxide ceramic is white and a much cheaper option if the application doesn't need the highest thermal performance. On the other hand, Aluminum Nitride (AIN) has a brown color and is a comparatively more expensive option but gives the best thermal performance.
Part 2: Ceramic PCB Conductor Materials
Ceramic core PCBs support the regular conductor materials of PCB manufacturing and their alloys. These key conductor materials are:
- Copper (Cu)
- Silver (Ag)
- Gold (Au)
- Platinum (Pt)
- Palladium (Pb)
Part 3: Types of Ceramic PCBs
From the level of substrates, ceramic PCBs include aluminum, AlN, BeO, Si3N4, hybrid substrate boards, etc. From the layers of the circuit boards, there are the single-layer, double-layer, and multilayer. Here we only put the ceramic PCB types according to the different ceramic substrates.
Alumina PCB
Advantages: cheap price, good thermal conductivity, and resistance, high hardness, high electrical insulation, strong corrosion resistance, high biocompatibility
Applications: LED lamps of white light, infrared, VCSEL
Aluminum oxide (Al₂O₃) PCB, or alumina PCB, is the most used ceramic PCB in the current market due to its cheaper price and nice properties. Alumina has good thermal conductivity and electrical resistance. For this reason, when alumina PCB is used, there is no need for adding an insulation layer. Alumina PCBs are mainly used for LEDs of 3W to 5W power. Why? Because the thermal conductivity is not that good to meet the high-power devices' demands.
Alumina has a higher thermal expansion coefficient than semiconductors. So you can't expect to use alumina PCBs for large-scale integrated circuits. But in general, if your devices do have not very high power requirements, alumina PCB is good enough.
In the alumina PCB market, there are 75%, 96%, and 99% alumina PCBs—the higher purity, the better properties, and also, the higher costs. PCBONLINE uses 96% alumina to manufacture alumina PCBs. Why? Because this is for a balance between quality and manufacturing cost. From the below table, you will find that 96% and 99% alumina have not so many differences in properties.
Characteristics
|
96% alumina
|
99% alumina
|
Color/Appearance
|
White/Dense
|
Beige/Dense
|
Density
|
3.6g/cm³
|
3.9g/cm³
|
Hardness
|
1500HV
|
1700HV
|
Warpage
|
≤0.3mm
|
≤0.2mm
|
Parallelism
|
±0.4%
|
±0.3%
|
Bending Resistance
|
3000Kgf/cm²
|
3500Kgf/cm²
|
Compressive Strength
|
25000Kgf/cm²
|
30000Kgf/cm²
|
Fracture Toughness
|
3-4Mpa m1/2
|
4Mpa m1/2
|
Thermal Conductivity
|
25W/(m·K)
|
31.4W/(m·K)
|
Voltage Resistance
|
18KV
|
18KV
|
Dielectric Constant [1MHz, 25°C]
|
9.4
|
10
|
Surface Roughness Ra
|
0.6-0.8μm
|
0.6-0.8μm
|
Water Absorption
|
0%
|
0%
|
Sintering Temperature
|
1689°C
|
1700°C
|
Volume Resistivity
|
/
|
/
|
Thermal Shock Resistance
|
200T°C
|
220T°C
|
Thermal Expansion Coefficient [20°C to 300°C]
|
6-7.5×10ˆ(-6)°C
|
8-10×10ˆ(-6)°C
|
Maximum Use Temperature
|
1400°C
|
1600°C
|
Aluminum Nitride PCB
Advantages: higher thermal conductivity and resistance, high hardness, high mechanical strength, higher electrical insulation, strong corrosion resistance, high biocompatibility, thermal expansion coefficient close to Si
Applications: high-power LEDs, power modules, laser fields
Aluminum nitride PCBs, or AlN PCBs, have times higher thermal conductivity than alumina PCBs. Why thermal conductivity is mentioned first and so many times? Because it is the most important property to evaluate ceramic PCBs.
Aluminum nitride PCBs are considered the most promising ceramic PCBs in the future. Using them, the thermal is dissipated from the ICs and other expensive components immediately. So high-power devices, such as LED ship lights, truck lamps, solar battery modules, large-scale integrated circuits, and so on adopt AlN PCBs as their base plates. Thermal doesn't accumulate in their chips so the devices work properly at high currents and for long periods.
Another reason that AlN PCBs are welcome for high-power LEDs and power modules is the similar thermal expansion coefficient with semiconductors Si. The chips of these high-power devices are made of Si. Thanks to the similar thermal expansion coefficients, the chips won't fall off the AlN PCB base plate during thermal deformation.
You can see more characteristics of AlN PCBs in the below table.
Characteristics
|
Values
|
Thermal Conductivity
|
170-320W/(m·K)
|
Volume Resistivity
|
>10ˆ13Ω·cm
|
Dielectric Constant [1MHz, 25°C]
|
9
|
Dielectric Loss [1MHz, 25°C]
|
3.8×10ˆ-4
|
Dielectric Strength
|
17KV/mm
|
Density
|
≥3.3g/cm³
|
Surface Roughness Ra
|
0.3-0.5μm
|
Thermal Expansion Coefficient [20°C to 300°C]
|
4.6×10ˆ-6°C
|
Fracture Toughness
|
320-330MPa m1/2
|
Elastic Modulus
|
310-320GPa
|
Moh's Hardness
|
8
|
Water Absorption
|
0%
|
Warpage
|
0.03-0.05mm
|
Maximum Use Temperature
|
2500°C
|
Silicon Nitride PCB
Advantages: high thermal conductivity, high strength, high fracture toughness
Applications: IGBT modules, vehicle-scale modules, military, aerospace, and aviation modules
Unlike the fragile traditional ceramic materials, under high temperatures, silicon nitride PCBs or Si₃N₄ PCBs have good mechanical strength and fracture toughness. Also, Si₃N₄ PCBs have high thermal conductivity (80+W/mK). Besides, silicon nitride PCBs have matched thermal expansion coefficient with Si.
As you know, IGBT modules for vehicles require much higher thermal conductivity than industrial-class IGBTs. And Vehicle modules are working in vibrating environments. For safety, the material for cars should also have good impact resistance.
So silicon nitride PCBs are used from vehicle-class modules. For the same reasons, military, aerospace, and aviation modules adopt Si₃N₄ PCBs.
However, the manufacturing of silicon nitride PCBs is not that easy. When the circuit layer is sputtered onto the silicon nitride substrate, the combination is not that stable. In other words, the circuit layer may fall off the ceramic substrate. Thankfully, PCBONLINE has successful manufacturing experience with silicon nitride PCBs for vehicle-class IGBT modules.
The last drawback of silicon nitride PCBs is the lower electrical resistance and insulation than other ceramic PCBs. So when you are designing a Si₃N₄ PCB project, remember this.
Silicon Carbide PCB
Advantages: good strength even at 1400°C, extremely high thermal conductivity, and resistance, good semiconductor electrical conductivity, high hardness
Applications: laser fields
Silicon carbon (SiC) is, diamond, but only the different carbon ratios. So silicon carbide PCBs have an extremely high thermal resistance. Working at 1000°C is easy for SiC PCBs. That's why they can be used in laser fields.
SiC has the property Si, so it has close characteristics of semiconductors. In other words, unlike other ceramic PCBs, a SiC PCB doesn't have high insulation.
The manufacturing of SiC PCBs is extremely expensive currently. But in the future, when the manufacturing technology moves forward, we can expect more applications of silicon carbide PCBs.
This is a thermal conductivity table of the different ceramic PCB substrates.
Ceramic Substrate Material
|
Thermal Conductivity
|
Aluminum Nitride (AIN)
|
150 – 180 W/mK
|
Aluminum Oxide(Alumina) (Al₂O₃)
|
18 – 36 W/mK
|
Beryllium Oxide (BeO)
|
184 – 300 W/mK
|
Boron Nitride (BN)
|
15 – 600 W/mK
|
Silicon Carbide (SiC)
|
70 – 210 W/mK
|
Part 4: Advantages Properties of Ceramic PCB
- Good thermal conductivity compared to FR4 PCBs.
- Very low thermal expansion coefficient.
- A better choice for high-temperature applications.
- Better thermal cycling performance.
- No heavy metal contaminants (PB, Hg, and Cr) in the PCB.
- High electrical isolation strength.
- No additional insulation layers are required compared to metal core PCBs.
Part 5: Applications of Ceramic PCBs
Due to the above-mentioned properties, ceramic PCBs are used for applications where strict performance is required. Generally, ceramic PCBs are for military applications, space program components, high-power laser applications, etc. But with manufacturing process improvements and reduced costs, they are also entering general industry applications, where more thermal performance is required.
PCBONLINE - High-Quality Ceramic PCB Manufacturer
PCBONLINE is a leading manufacturer of ceramic printed circuit boards. Over the past decades of manufacturing and assembly in ceramic PCBs, we've accumulated rich experience. We provide high-quality alumina PCBs, aluminum nitride PCBs, DOB LEDs, LED COBs, IGBT ceramic substrate boards, 3D alumina products, etc.
Below is the LED COB module that PCBONLINE manufactured for clients. You are welcome to get an online quote or contact us by email at info@pcbonline.com. Free design and manufacturing plus one-on-one engineering support will bring out the highest quality of your ceramic PCBs.