This blog will solve your problems with PCB prototypes and preparation before production. This blueprint will lay a foundation for subsequent manufacturing. What is PCB prototype assembly? What aspects need to be noticed more?
To find out more please see below:
Part 1: What is PCB Prototype
PCB prototype is the basic step before PCB production.
This is a kind of design, normally, if we find there are mistakes in the process of production then the designer needs to redesign the whole PCB circuits, which will lead to more time wasted.
After the design, you need to send it to PCB manufacturers, if you asked for PCB assembly, then the factory will produce PCB board first, PCB board includes:
- Copper – Copper layer is added on both sides of the PCB if it's double-sided and on one side if it's single-sided.
- Substrate – The base fabric gives the PCB its firmness. It protects the board from breaking for added durability and functionality.
- Solder paste – a solder mask is added on top of the copper layer, the mask insulates the copper and prevents it from being in contact with other conductive fabrics. Any contact with conductive materials can result in a circuit short.
- Silkscreen – Basically, this happened on the final and top layer of the PCB board. It forms the symbols and characters on the board, which helps in indicating the functionality of every component, which can prevent confusion and errors.
Part 2: The Technology Using in the PCB Prototype Assembly Process
The PCB assembly is a long, critical process that involves a myriad of manual and automated steps. There are three crucial technologies used in the PCB assembly process: THT, SMT, and mixed.
1. THT (Through Hole Technology)
Through-Hole Technology, abbreviation: THT. Through-hole PCB assembly is to insert components into the circuit board and then solder them firmly.
The THT involves three essential steps which include:
Placement of Components
This is a manual process that is explicitly done by professional engineers.
The components are required to be placed precisely and quickly in the corresponding positions.
This can only be done by highly trained experts to avoid errors.
The process is required to adhere to operational standards and regulations of the THT mounting process to get an excellent end product.
Inspection
After the completion of component placements, the PCB board will be inspected to determine if the components were accurately positioned.
The inspection will help to determine if there are faults and get them rectified instantly.
Soldering
Once the inspection is done and every component is accurately positioned, it will be soldered on the circuit board. In this process, the board will move slowly over a liquid solder at approximately 500°F.
2.SMT(Surface Mount Technology)
SMT is the abbreviation of Surface Mounting Technology, which is the most popular technology and process in the electronic assembly industry.
It is a circuit connection technology that surfaces components such as no-leads, short-leads, or BGA (SMC/SMD for short) are mounted on the surface of a Printed Circuit Board (PCB) or other substrates, and welded and assembled by reflow soldering or immersion soldering. The process takes place in 3 critical stages:
Mounting Components
The components are placed on the board through reels. These reels are designed to rotate to ensure the parts are quickly sticking onto the board.
Note
In the SMT assembly process, regular maintenance of the SMT machine is critical, this can make the automated process quite efficient and will lead to few or even no errors at all.
Soldering (reflow)
Once the components are positioned accurately, the board will pass through a furnace at 500°F. It ensures the solder paste is heated and melted down to form sturdy joints between the board and the components.
The process is accomplished through a reflow oven that helps the components get held firmly on the board.
SMT has a high automation degree with a myriad of benefits:
- lower cost
- Minimize human error rate
- Ensure high quality
- Save time for mass production
Some of the industries that utilize this automation process include aviation, wireless, telecommunication, and automotive.
Optical Inspection
Any board that goes through a reflow cycle is sent for an inspection.
The inspection detects any issues on the board and also helps in determining the root cause of any error.
3. Mixed Technology
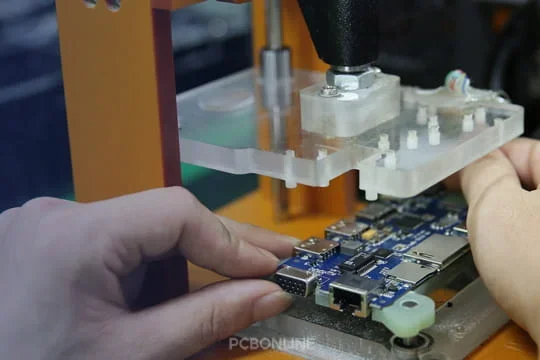
Mixed technology is a combination of THT and SMT assembly processes to form a sturdy, reliable PCB.
Electronic devices are becoming more complicated day by day, which means products will require more sophisticated PCB boards in the future.
It’s increasingly becoming impossible for PCBs assembled in a single process to perform multifaceted tasks. As a result, mixed technology is the only viable solution.
Question
Where can I find a professional PCB prototype manufacturer with the best price?
PCBONLINE provides various assembly solutions including low volume, medium volume, high volume, consigned, turnkey, and SMT and THT PCB assembly.
You can get your customized PCB assembly in as fast as 24 hours perfectly tailored to your business needs.
Regarding certification, we implement the ISO9001:2015 international standard quality management system to bring out the best assembly quality.
What’s more, in PCBONLINE, advanced machines and technology are used, such as 30 Panasonic and Yamaha SMT lines, Germany ERSA selective wave soldering, solder paste detection 3DSPI, AOI, X-ray, etc.